Elastic deformation and vibration suppression method for robot grinding and polishing of aircraft composite components
A robot processing and elastic deformation technology, which is applied in the direction of automatic grinding control devices, metal processing equipment, grinding machine parts, etc. Effect
- Summary
- Abstract
- Description
- Claims
- Application Information
AI Technical Summary
Problems solved by technology
Method used
Image
Examples
Embodiment Construction
[0057] In order to make the object, technical solution and advantages of the present invention clearer, the present invention will be further described in detail below in conjunction with the accompanying drawings and embodiments. It should be understood that the specific embodiments described here are only used to explain the present invention, not to limit the present invention. In addition, the technical features involved in the various embodiments of the present invention described below can be combined with each other as long as they do not constitute a conflict with each other.
[0058] Such as figure 1 As shown, the embodiment of the present invention provides a method for elastic deformation and vibration suppression of aircraft composite component robotic grinding and polishing, which mainly includes two aspects: one is elastic deformation control of aircraft composite component robotic grinding and polishing. First, the parameters of the grinding process were used a...
PUM
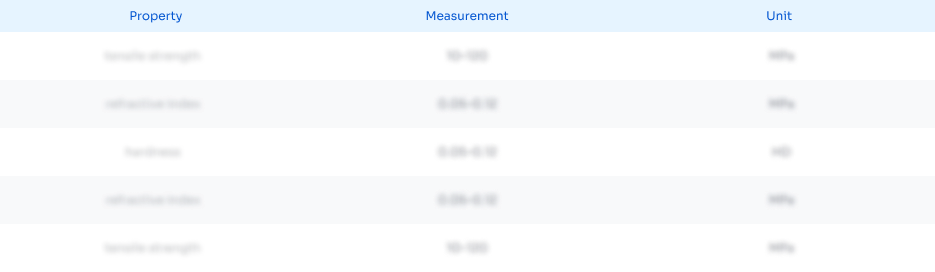
Abstract
Description
Claims
Application Information

- Generate Ideas
- Intellectual Property
- Life Sciences
- Materials
- Tech Scout
- Unparalleled Data Quality
- Higher Quality Content
- 60% Fewer Hallucinations
Browse by: Latest US Patents, China's latest patents, Technical Efficacy Thesaurus, Application Domain, Technology Topic, Popular Technical Reports.
© 2025 PatSnap. All rights reserved.Legal|Privacy policy|Modern Slavery Act Transparency Statement|Sitemap|About US| Contact US: help@patsnap.com