Forming mechanism of paper pulp molding equipment
A pulp molding and forming mechanism technology, applied in textiles and papermaking, etc., can solve the problems of overflow splashing, sedimentation pulp, insufficient pulp volume, etc., and achieve the effect of ensuring product quality and uniform concentration
- Summary
- Abstract
- Description
- Claims
- Application Information
AI Technical Summary
Problems solved by technology
Method used
Image
Examples
Embodiment Construction
[0030] The specific implementation of this embodiment will be described below in conjunction with the accompanying drawings.
[0031] Such as Figure 1 to Figure 10 As shown, the molding mechanism of the pulp molding equipment of this embodiment includes a frame 1 connected to the pulp tank 2, and the frame 1 is located above the pulp tank 2 and connected to the upper mold 3, and the pulp tank 2 is passed through a partition 21 is divided into an inner chamber 22 and an outer chamber 23, the inner chamber 22 is connected to the slurry inlet pipe 24, the outer chamber 23 is connected to the overflow pipe 25, the partition 21 includes a vertical section 211, and the lower end of the vertical section 211 is connected to a downward slope Section 212, the lower inclined section 212 is inclined towards the central direction of the pulp tank 2, and the partition plate 21 is located at the upper end of the vertical section 211 to connect the upwardly inclined upper inclined section 21...
PUM
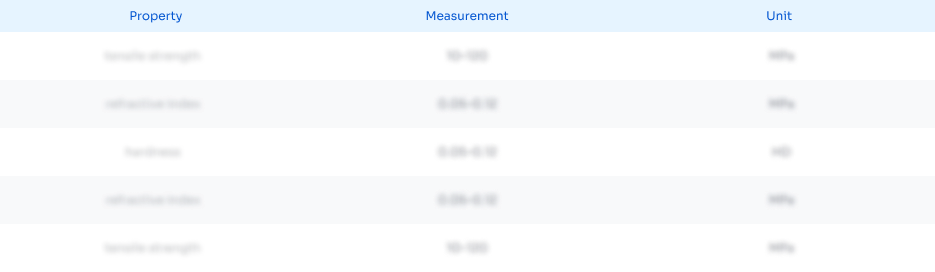
Abstract
Description
Claims
Application Information

- R&D
- Intellectual Property
- Life Sciences
- Materials
- Tech Scout
- Unparalleled Data Quality
- Higher Quality Content
- 60% Fewer Hallucinations
Browse by: Latest US Patents, China's latest patents, Technical Efficacy Thesaurus, Application Domain, Technology Topic, Popular Technical Reports.
© 2025 PatSnap. All rights reserved.Legal|Privacy policy|Modern Slavery Act Transparency Statement|Sitemap|About US| Contact US: help@patsnap.com