Composite material T shaped ribbed wallboard autoclave forming die structure and forming method
A technology of autoclave forming and composite materials, which is applied to household components, household appliances, other household appliances, etc., can solve the problems of resin enrichment, no solution, lack of glue, etc., to avoid adhesion and reduce the difficulty of demolding , Guarantee the effect of product quality
- Summary
- Abstract
- Description
- Claims
- Application Information
AI Technical Summary
Problems solved by technology
Method used
Image
Examples
Embodiment 1
[0025] Such as Figure 1-Figure 2 As shown, a composite material T-shaped reinforced wall plate autoclave forming mold structure includes a mold 1 provided with a T-shaped groove 3, and the T-shaped groove 3 is used to make a composite material T-shaped reinforced wall plate;
[0026] The T-shaped rib 6 is placed in the mold 1 with the T-shaped groove 3, and accurately positioned with the mold 1 through the positioning hole, and a sealing strip 5 is designed between the T-shaped rib 6 and the mold 1;
[0027] Sealing grooves 2 are arranged on the groove walls on both sides of the T-shaped groove 3, and sealing strips 5 are installed in the sealing grooves 2. The sealing strips 5 can prevent the resin from flowing during the curing process of the prepreg 9, resulting in local lack of resin and preventing resin from flowing in. In the groove, the difficulty of demoulding is reduced and the product quality is guaranteed;
[0028] The T-shaped ribs 6 are dry ribs, and the wet ski...
Embodiment 2
[0030] In this embodiment, a positioning hole A is provided on the T-shaped rib 6, and a positioning hole B is obtained by drilling a hole on the mold 1. The positioning hole A and the positioning hole B are used together to ensure that the T-shaped rib 6 is accurately installed on the mold 1. superior.
[0031] The T-shaped rib 6 includes a web and an edge, and the T-shaped rib 6 web is inserted into the bottom of the T-shaped groove 3 of the mold 1, and the edge is placed on the mold 1.
[0032] The positioning hole A of the T-shaped rib 6 is arranged on the flange, the number of the positioning hole A is two, and the position and quantity of the positioning hole B cooperate with the positioning hole A.
[0033] The T-shaped rib 6 is placed in the mold 1 with the T-shaped groove 3, and accurately positioned with the mold 1 through the positioning holes (including the positioning hole A and the positioning hole B) to ensure the accuracy of installation. The T-shaped groove 3...
Embodiment 3
[0035] In order to solve the problem of mass production and improve efficiency. A plurality of T-shaped grooves 3 can be arranged on the mold 1 of the present solution, and the T-shaped grooves 3 are spaced apart by a certain distance.
[0036] The T-shaped grooves 3 are arranged in one or more rows; when the T-shaped grooves 3 are arranged in multiple rows, the T-shaped grooves 3 form a groove matrix, which is used to make a reinforced wall panel with a plurality of T-shaped ribs 6 .
[0037] Mold 1 is a cylinder as a whole, and some T-shaped grooves 3 are arranged on the side wall of mold 1, and are used for making the integral composite barrel section 13 (such as Figure 9 shown).
[0038] Through this embodiment, not only can obtain single composite material T-shaped reinforced panel 11 (such as Image 6 shown) can also obtain multi-composite material T-shaped reinforced wall panels 12 (such as Figure 7 shown), and include T-stiffened panels for integral composite bar...
PUM
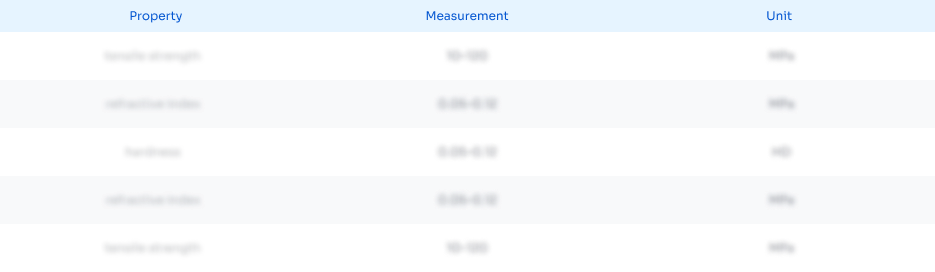
Abstract
Description
Claims
Application Information

- R&D
- Intellectual Property
- Life Sciences
- Materials
- Tech Scout
- Unparalleled Data Quality
- Higher Quality Content
- 60% Fewer Hallucinations
Browse by: Latest US Patents, China's latest patents, Technical Efficacy Thesaurus, Application Domain, Technology Topic, Popular Technical Reports.
© 2025 PatSnap. All rights reserved.Legal|Privacy policy|Modern Slavery Act Transparency Statement|Sitemap|About US| Contact US: help@patsnap.com