Surface treatment method of die steel after molding
A processing method and technology of die steel, applied in the direction of manufacturing tools, grinding machines, grinding machine parts, etc., can solve the problems of inability to ensure sufficient contact of the surface of die steel, increase the operating cost of manufacturers, wear the surface of die steel, etc., to save operation. Cost, easy cleaning, guaranteed thorough results
- Summary
- Abstract
- Description
- Claims
- Application Information
AI Technical Summary
Problems solved by technology
Method used
Image
Examples
Embodiment Construction
[0037] The embodiments of the present invention will be described in detail below with reference to the accompanying drawings, but the present invention can be implemented in many different ways defined and covered by the claims.
[0038] Such as Figure 1 to Figure 9 As shown, a method for surface treatment of mold steel after forming uses a kind of oxide layer cleaning equipment. The oxide layer cleaning equipment includes a substrate 1, a shell 2 and a cleaning device 3. The specific process for cleaning the scale is as follows:
[0039] S1. Equipment adjustment: Adaptively adjust the position of the corresponding structure of the device according to the thickness of the mold steel;
[0040] S2. mold steel transmission: the mold steel to be cleaned is delivered to the cleaning device 3 one by one;
[0041] S3. oxide layer cleaning: the oxide layer on the surface of the model steel is cleaned by the cleaning device 3;
[0042] S4. Material discharge: take out the cleaned mo...
PUM
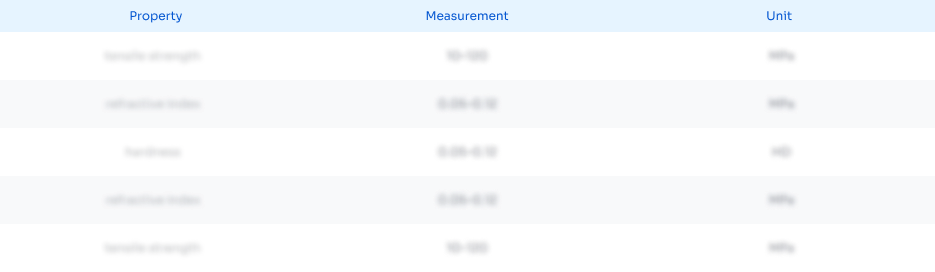
Abstract
Description
Claims
Application Information

- R&D
- Intellectual Property
- Life Sciences
- Materials
- Tech Scout
- Unparalleled Data Quality
- Higher Quality Content
- 60% Fewer Hallucinations
Browse by: Latest US Patents, China's latest patents, Technical Efficacy Thesaurus, Application Domain, Technology Topic, Popular Technical Reports.
© 2025 PatSnap. All rights reserved.Legal|Privacy policy|Modern Slavery Act Transparency Statement|Sitemap|About US| Contact US: help@patsnap.com