Multi-joint heavy-load hydraulic robot system and high-precision motion control method
A hydraulic robot, multi-joint technology, applied in the direction of program control manipulators, manipulators, manufacturing tools, etc., can solve the problems of strong nonlinearity and model uncertainty, difficult to prove stability, robot system parameters and disturbance uncertainty.
- Summary
- Abstract
- Description
- Claims
- Application Information
AI Technical Summary
Problems solved by technology
Method used
Image
Examples
Embodiment Construction
[0065] In order to make the object, technical solution and advantages of the present invention clearer, the present invention will be further described in detail below in conjunction with the accompanying drawings and specific embodiments.
[0066] as attached figure 1 As shown, the five-degree-of-freedom heavy-duty hydraulic robot proposed by the present invention includes: base 1, crank arm hydraulic cylinder 2, crank arm 3, boom 4, small arm hydraulic cylinder 5, swing arm hydraulic cylinder 6, swing arm 7, An end effector 8, a rotary hydraulic cylinder 9, a small arm 10, a large arm hydraulic cylinder 11, a pump source unit, a control valve unit, a power amplification unit, a real-time controller, and a sensor detection unit. The base 1 is connected to the crank arm hydraulic cylinder 2 through a bearing seat, and the displacement sensor measures the linear displacement of the piston rod of the crank arm hydraulic cylinder 2. The base 1 is connected to the crank arm 3 thro...
PUM
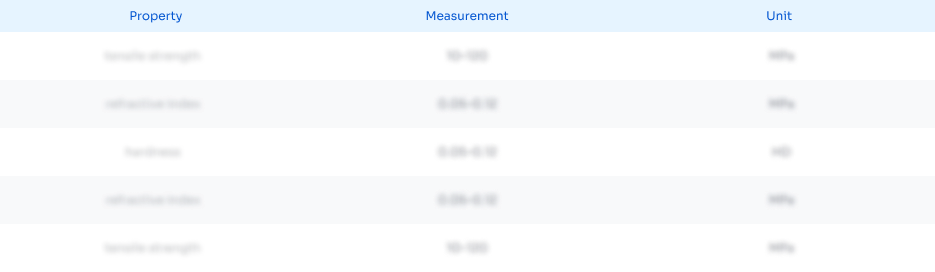
Abstract
Description
Claims
Application Information

- R&D Engineer
- R&D Manager
- IP Professional
- Industry Leading Data Capabilities
- Powerful AI technology
- Patent DNA Extraction
Browse by: Latest US Patents, China's latest patents, Technical Efficacy Thesaurus, Application Domain, Technology Topic, Popular Technical Reports.
© 2024 PatSnap. All rights reserved.Legal|Privacy policy|Modern Slavery Act Transparency Statement|Sitemap|About US| Contact US: help@patsnap.com