Calibration method and device for relative spatial position relation of multiple robots
A multi-robot, relative space technology, applied in manipulators, program-controlled manipulators, manufacturing tools, etc., can solve problems such as rising costs, unfavorable engineering operations, and exceeding the measurement range of 3D sensors, so as to eliminate calibration errors, improve universality, The effect of reducing the amount of calculation
- Summary
- Abstract
- Description
- Claims
- Application Information
AI Technical Summary
Problems solved by technology
Method used
Image
Examples
Embodiment Construction
[0039] In order to better explain the present invention and facilitate understanding, the present invention will be described in detail below through specific embodiments in conjunction with the accompanying drawings.
[0040] The calibration method and calibration device for the relative spatial position relationship of multiple robots proposed in the embodiments of the present invention make full use of the 3D sensors at the end of each robot, and perform hand-eye calibration on the 3D sensors on each robot to obtain the relative spatial position of each 3D sensor. The position conversion relationship of the corresponding robot end, and collect the 3D point cloud data of the calibration object placed in the multi-robot co-working space through the 3D sensor on each robot to obtain the measurement position coordinates of the calibration object in the corresponding 3D sensor At the same time, when the 3D sensor on each robot collects the 3D point cloud data of the calibration o...
PUM
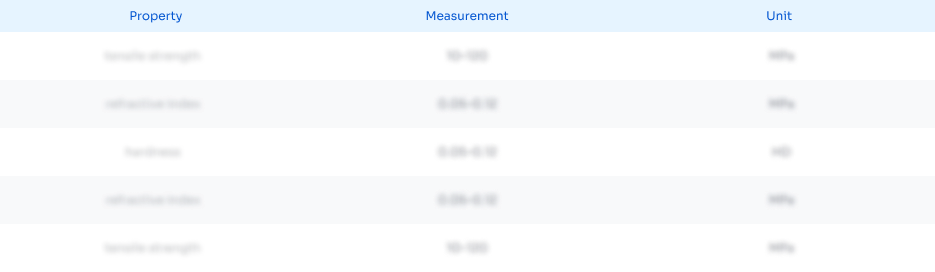
Abstract
Description
Claims
Application Information

- R&D Engineer
- R&D Manager
- IP Professional
- Industry Leading Data Capabilities
- Powerful AI technology
- Patent DNA Extraction
Browse by: Latest US Patents, China's latest patents, Technical Efficacy Thesaurus, Application Domain, Technology Topic, Popular Technical Reports.
© 2024 PatSnap. All rights reserved.Legal|Privacy policy|Modern Slavery Act Transparency Statement|Sitemap|About US| Contact US: help@patsnap.com