Method for improving coil shape quality of hot rolled strip steel
A hot-rolled strip and coil technology, used in metal rolling, metal rolling, rolling mill control devices, etc., can solve the problems of increasing the secondary expansion stroke, equipment structure restrictions, etc., to improve the coil shape and increase production. Efficiency, the effect of avoiding plate unevenness and defective products
- Summary
- Abstract
- Description
- Claims
- Application Information
AI Technical Summary
Problems solved by technology
Method used
Image
Examples
Embodiment Construction
[0032] The present invention will be described in detail below, but it should be pointed out that the implementation of the present invention is not limited to the following embodiments.
[0033] A method for improving the coil shape quality of hot rolled strip steel includes:
[0034] 1) Calculation of the tail point position of the parking position at the tail of the strip
[0035] After the head of the coiler bites the steel, the tail stop state will be set after a delay of 21-36 seconds. When the tail of the strip is detected to leave the pinch roller after the tail is thrown, the tail automatic stop control starts, and the reel will stop according to the deceleration curve ;
[0036] a) After the pinch roll of 1# coiler bites the steel, it will start to calculate the position of the tail point after a delay of 21-36 seconds. The calculation is completed after the steel is thrown in the F7 frame, and the tail program is set at the same time when the coil is stopped. After the coi...
PUM
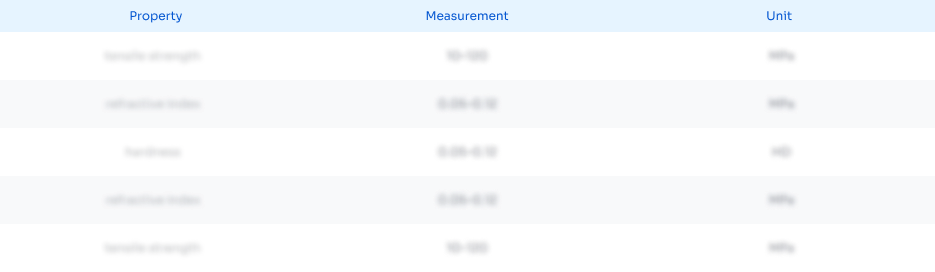
Abstract
Description
Claims
Application Information

- Generate Ideas
- Intellectual Property
- Life Sciences
- Materials
- Tech Scout
- Unparalleled Data Quality
- Higher Quality Content
- 60% Fewer Hallucinations
Browse by: Latest US Patents, China's latest patents, Technical Efficacy Thesaurus, Application Domain, Technology Topic, Popular Technical Reports.
© 2025 PatSnap. All rights reserved.Legal|Privacy policy|Modern Slavery Act Transparency Statement|Sitemap|About US| Contact US: help@patsnap.com