Machining technology of ultra-precision part of CVD equipment
A processing technology and ultra-precision technology, applied in welding equipment, metal processing equipment, electron beam welding equipment, etc., can solve problems such as the inability to guarantee ultra-high precision requirements
- Summary
- Abstract
- Description
- Claims
- Application Information
AI Technical Summary
Problems solved by technology
Method used
Image
Examples
Embodiment Construction
[0015] The following is attached with the manual figure 1 And embodiment the present invention is described in further detail.
[0016] A processing technology plan for ultra-precision parts, which combines precision machining, precision electron beam welding, ultra-high cleanliness cleaning technology, ultra-thick hard anode surface treatment technology and other technologies to complete the manufacture of an ultra-precision part.
[0017] The ultra-precision machining requires 1 pre-welding processing and 2 post-welding processing to ensure the dimensional accuracy of the parts: flatness parallelism 0.01-0.03mm, sealing groove Ra0.4-Ra0.8mm, pin hole position degree 0.03 mm-0.05mm etc.
[0018] The precision electron beam welding needs to complete the welding of one side and one seam first, remove the reinforcement height of 0.5mm-1mm, and then process the second welding chamber for the second welding. Otherwise, the other welds will collapse because the welds interfere wi...
PUM
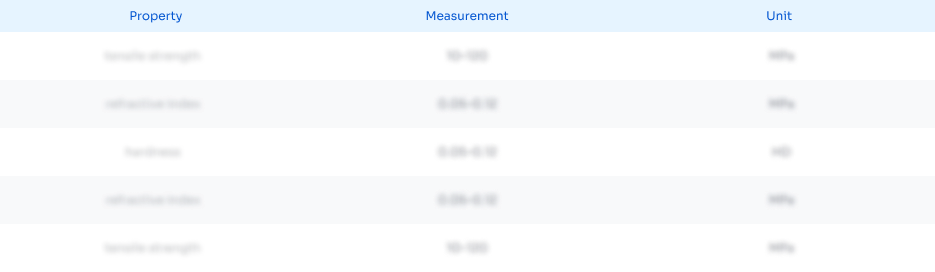
Abstract
Description
Claims
Application Information

- R&D
- Intellectual Property
- Life Sciences
- Materials
- Tech Scout
- Unparalleled Data Quality
- Higher Quality Content
- 60% Fewer Hallucinations
Browse by: Latest US Patents, China's latest patents, Technical Efficacy Thesaurus, Application Domain, Technology Topic, Popular Technical Reports.
© 2025 PatSnap. All rights reserved.Legal|Privacy policy|Modern Slavery Act Transparency Statement|Sitemap|About US| Contact US: help@patsnap.com