Power battery tab heat dissipation system capable of exhausting waste gas
A power battery and heat dissipation system technology, applied in secondary batteries, exhaust plug devices, battery pack components, etc., can solve the problems of low thermal conductivity of diaphragm materials, large energy consumption of auxiliary components, uneven flow field, etc. Enhance the heat transfer rate, make up for dimensional tolerances, and inhibit the effect of heat diffusion
- Summary
- Abstract
- Description
- Claims
- Application Information
AI Technical Summary
Problems solved by technology
Method used
Image
Examples
Embodiment Construction
[0017] The present invention is described in more detail below in conjunction with accompanying drawing example:
[0018] combine figure 1 , the present invention provides a power battery tab heat dissipation system that can exhaust exhaust gas. On the basis of not changing the original heat management system, it combines the advantages of air cooling and liquid cooling heat management methods, effectively solving the traditional liquid cooling heat management method The disadvantage of being unable to exhaust the exhaust gas generated in the thermal management system; at the same time, using the thermal management method of battery tab heat dissipation can efficiently dissipate heat from the battery module and further improve the temperature uniformity of the system; multi-layer safety protection is set in the system, It can better avoid the current frequent battery thermal runaway problem and promote the development of new energy hybrid and pure electric vehicles.
[0019] ...
PUM
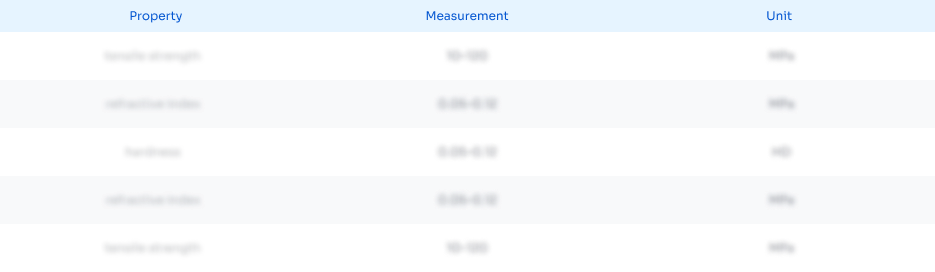
Abstract
Description
Claims
Application Information

- Generate Ideas
- Intellectual Property
- Life Sciences
- Materials
- Tech Scout
- Unparalleled Data Quality
- Higher Quality Content
- 60% Fewer Hallucinations
Browse by: Latest US Patents, China's latest patents, Technical Efficacy Thesaurus, Application Domain, Technology Topic, Popular Technical Reports.
© 2025 PatSnap. All rights reserved.Legal|Privacy policy|Modern Slavery Act Transparency Statement|Sitemap|About US| Contact US: help@patsnap.com