Melt direct processing caprolactam polymerization method
A technology of caprolactam and polymerization method, which is applied in the field of nylon materials, can solve the problems of low polymer number average molecular weight, slow reaction speed, and oligomer control, and achieve the effects of reducing energy consumption, improving utilization rate, and simple process
- Summary
- Abstract
- Description
- Claims
- Application Information
AI Technical Summary
Problems solved by technology
Method used
Image
Examples
Embodiment 1
[0063] The first step: at a temperature of 75°C, caprolactam, HOOC (CH 2 ) 4 COOH, deionized water and NH 2 (CH 2 ) 4 COOH was mixed in proportion, and stirred for 60min under the condition of mechanical stirring (60r / min); the amount of deionized water added was 1.5wt% relative to caprolactam, and HOOC(CH 2 ) 2 The amount of COOH added is 0.4wt%, NH 2 (CH 2 ) 4 The amount of COOH added is 0.8wt%;
[0064] The second step: After the mixture obtained in the first step is heated by the melt pump and the pre-heater, it is transported to the ring-opening kettle for ring-opening reaction. The polymerization temperature is controlled at 213 ° C, and the polymerization pressure is controlled at 1.8 MPa; the reaction time is The 0.7h prepolymer is transported to the top of the tower by a melt pump, mixed with fresh caprolactam, and the reflux flow is 1.8wt% of the caprolactam flow. When the following conditions are met, the reaction is terminated: the number average molecular...
Embodiment 2
[0069] The first step: at a temperature of 138°C, caprolactam, HOOC (CH 2 ) 8 COOH, deionized water and nylon 66 salt were mixed in proportion, and stirred for 15 minutes under the condition of mechanical stirring (200r / min); the amount of deionized water added was 3.5wt% relative to caprolactam, HOOC(CH 2 ) 8 The amount of COOH added is 0.12wt%, and the amount of nylon 66 salt added is 0.03wt%;
[0070] The second step: After the mixture obtained in the first step is heated by the melt pump and the pre-heater, it is transported to the ring-opening kettle for ring-opening reaction. The polymerization temperature is controlled at 258 ° C, and the polymerization pressure is controlled at 0.3 MPa; the reaction time is The 1.4h prepolymer is transported to the top of the tower by a melt pump, mixed with fresh caprolactam, and the reflux flow is 0.48wt% of the caprolactam flow. When the following conditions are met, the reaction is terminated: the number average molecular weight...
Embodiment 3
[0075] The first step: at a temperature of 95°C, caprolactam, terephthalic acid, deionized water and NH 2 (CH 2 ) 4 COOH was mixed in proportion, and stirred for 45 minutes under the condition of mechanical stirring (120r / min); among them, relative to caprolactam, the amount of deionized water added was 2.3wt%, the amount of terephthalic acid added was 0.33wt%, and the amount of NH 2 (CH 2 ) 4 The amount of COOH added is 0.47wt%;
[0076] The second step: After the mixture obtained in the first step is heated by the melt pump and the pre-heater, it is transported to the ring-opening kettle for ring-opening reaction. The polymerization temperature is controlled at 228 ° C, and the polymerization pressure is controlled at 0.9 MPa; the reaction time is The 1.3h prepolymer is transported to the top of the tower by a melt pump, mixed with fresh caprolactam, and the reflux rate is 1.5wt% of the caprolactam flow rate. When the following conditions are met, the reaction is termin...
PUM
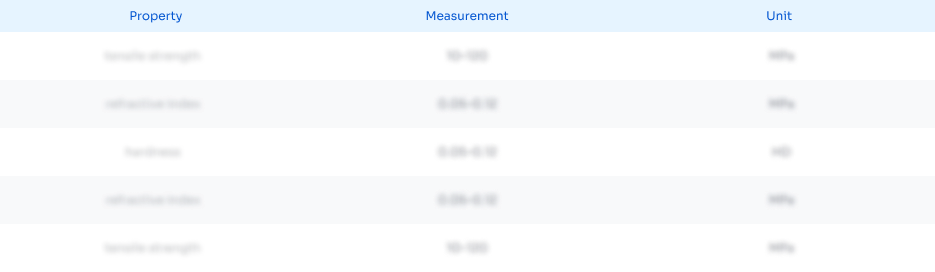
Abstract
Description
Claims
Application Information

- Generate Ideas
- Intellectual Property
- Life Sciences
- Materials
- Tech Scout
- Unparalleled Data Quality
- Higher Quality Content
- 60% Fewer Hallucinations
Browse by: Latest US Patents, China's latest patents, Technical Efficacy Thesaurus, Application Domain, Technology Topic, Popular Technical Reports.
© 2025 PatSnap. All rights reserved.Legal|Privacy policy|Modern Slavery Act Transparency Statement|Sitemap|About US| Contact US: help@patsnap.com