Machining process-oriented mobile robot system calibration method and system
A mobile robot, system calibration technology, applied in the direction of comprehensive factory control, general control system, control/regulation system, etc., can solve problems such as inability to meet on-site processing
- Summary
- Abstract
- Description
- Claims
- Application Information
AI Technical Summary
Problems solved by technology
Method used
Image
Examples
Embodiment Construction
[0078] Such as figure 1 As shown, the processing-oriented mobile robot system includes 840Dsl control cabinet, omnidirectional mobile platform, robot, processing tool, stable support, laser tracker, workpiece to be processed, etc. Around the mobile robot system, define the omnidirectional mobile platform coordinate system, the robot base coordinate system, the robot end flange coordinate system and the workpiece coordinate system.
[0079] Such as image 3 As shown, a process-oriented mobile robot system calibration method proposed by the present invention includes the following steps:
[0080] (1) Construct different coordinate systems based on laser tracker measurement;
[0081] The laser tracker is used to establish the coordinate system of the omnidirectional mobile platform, the base coordinate system of the robot, the coordinate system of the end flange of the robot and the coordinate system of the workpiece to be processed;
[0082] Such as figure 2 As shown, speci...
PUM
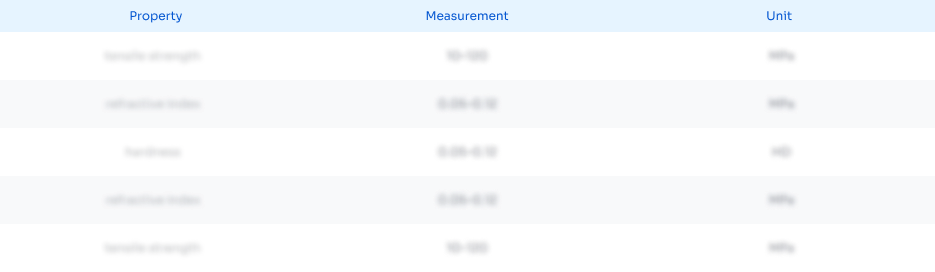
Abstract
Description
Claims
Application Information

- R&D
- Intellectual Property
- Life Sciences
- Materials
- Tech Scout
- Unparalleled Data Quality
- Higher Quality Content
- 60% Fewer Hallucinations
Browse by: Latest US Patents, China's latest patents, Technical Efficacy Thesaurus, Application Domain, Technology Topic, Popular Technical Reports.
© 2025 PatSnap. All rights reserved.Legal|Privacy policy|Modern Slavery Act Transparency Statement|Sitemap|About US| Contact US: help@patsnap.com