A Calibration Method for Quickly Determining the Geometric Positions of Each Component in a Deflection Measurement System
A technology of measurement system and calibration method, applied in the field of optical engineering, can solve the problem that the position of the workpiece cannot be directly determined
- Summary
- Abstract
- Description
- Claims
- Application Information
AI Technical Summary
Problems solved by technology
Method used
Image
Examples
Embodiment 1
[0039] In order to realize the quick and simple calibration of the deflection measurement system, the ordinary flat mirror is made into a standard part with its own reference for improvement. It is made of aluminum alloy, and the upper part is a cylinder with a diameter of 200mm and a height of 10mm. The upper surface is made of single-point diamond. Turned into a mirror surface, the flatness is better than λ / 5PV. Process 24 circular spots with a diameter of 16mm evenly distributed on the upper surface at φ180mm, one of which is set to a diameter of 10mm, and all the circular spots are blackened, such as figure 1 shown. The pose of the plane mirror is obtained directly through the landmark points on the plane mirror. The screen displays a 20×15 dot array, and the diameter of each dot is set to 15 pixels, according to image 3 Steps to complete the geometric calibration. Measure an aspherical workpiece with a caliber of 130mm, and perform ray tracing from the center of gravi...
PUM
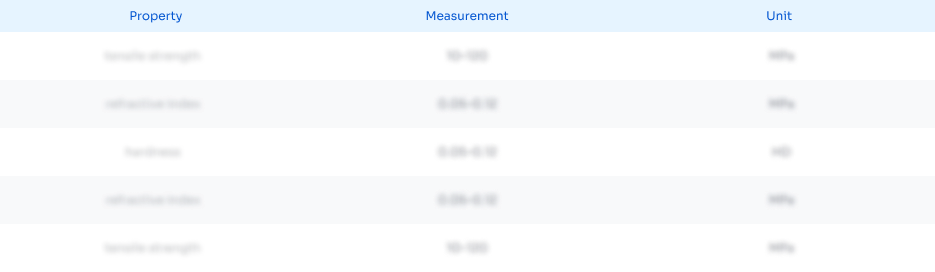
Abstract
Description
Claims
Application Information

- Generate Ideas
- Intellectual Property
- Life Sciences
- Materials
- Tech Scout
- Unparalleled Data Quality
- Higher Quality Content
- 60% Fewer Hallucinations
Browse by: Latest US Patents, China's latest patents, Technical Efficacy Thesaurus, Application Domain, Technology Topic, Popular Technical Reports.
© 2025 PatSnap. All rights reserved.Legal|Privacy policy|Modern Slavery Act Transparency Statement|Sitemap|About US| Contact US: help@patsnap.com