A Method for Measuring Wall Thickness of Hollow Turbine Blade Leading Edge
A technology of turbine blades and measurement methods, applied in the direction of measuring devices, instruments, and using wave/particle radiation, etc., can solve problems such as inaccurate measurement results, and achieve the effects of eliminating inaccurate measurement, eliminating amplification effects, and accurate measurement
- Summary
- Abstract
- Description
- Claims
- Application Information
AI Technical Summary
Problems solved by technology
Method used
Image
Examples
Embodiment
[0104] Step 1, make the blade bracket tooling: According to the data model of the hollow turbine blade, determine the tangent direction of the leading edge of the blade, convert the reference to the easy-to-clamp part, which is generally the tenon part, design and manufacture the bracket tooling to ensure the stable placement of the blade , the tangent direction of the leading edge of the blade is vertical, and the support tooling is as follows: Figure 16 , Figure 17 As shown, the vertebral head can be naturally placed on the tooling during use.
[0105] Step 2, select a stainless steel pipe with uniform diameter as a size standard block. The material of the pipe standard sample block is 1Cr18Ni9Ti, and the wall thickness is about 1mm.
[0106] Step 3, measure the inner diameter or outer diameter of the standard sample block of the pipe to obtain the standard value of the inner diameter or outer diameter. The reserved digits of the standard value are the same as the requir...
PUM
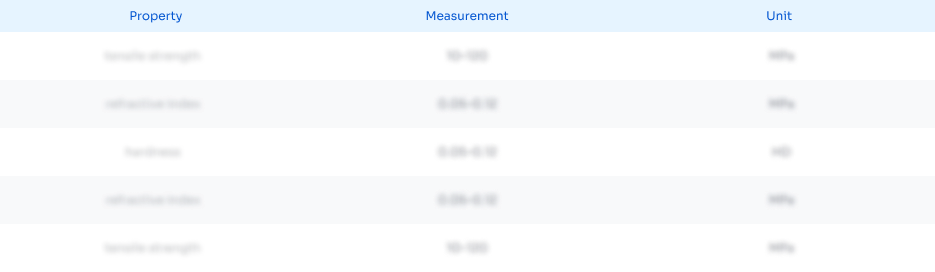
Abstract
Description
Claims
Application Information

- Generate Ideas
- Intellectual Property
- Life Sciences
- Materials
- Tech Scout
- Unparalleled Data Quality
- Higher Quality Content
- 60% Fewer Hallucinations
Browse by: Latest US Patents, China's latest patents, Technical Efficacy Thesaurus, Application Domain, Technology Topic, Popular Technical Reports.
© 2025 PatSnap. All rights reserved.Legal|Privacy policy|Modern Slavery Act Transparency Statement|Sitemap|About US| Contact US: help@patsnap.com