Energy-saving rosewood straightening process
A straightening and mahogany technology, applied in the straightening process of mahogany wood, can solve the problems of slow pyrolysis, high energy consumption, long heating time, etc., achieve pH balance, low energy consumption, and reduce pyrolysis. effect of time
- Summary
- Abstract
- Description
- Claims
- Application Information
AI Technical Summary
Problems solved by technology
Method used
Examples
Embodiment 1
[0019] Example 1. A kind of energy-saving mahogany straightening process, comprises the following steps,
[0020] a, soak the mahogany in the form of wooden cubes with 25% hydrochloric acid solution for 90 hours to get product A,
[0021] b. Soak product A with ammonia water until the wood acidity of product B reaches 6.8 to obtain product B.
[0022] c. Soak product B in running water for 3 days to obtain product C1; air-dry product C1 so that the moisture content of product C1 is 15% to obtain product C.
[0023] d. Put product C into a steam box to heat for 2.5 hours, and keep the water content of product C at 18% by adjusting the steam saturation in the steam box to obtain product D.
[0024] e. Put product D into a mold for straightening, and heat product D while straightening, so that the moisture content of product D is 10%, to obtain product E1; product E1 is cooled at room temperature, and left to stand for 4 hours to obtain a finished product.
Embodiment 2
[0025] Example 2. A kind of energy-saving mahogany straightening process, comprises the following steps,
[0026] a, soak the mahogany in the form of wooden cubes with 20% hydrochloric acid solution for 100 hours to get product A,
[0027] b. Soak product A with ammonia water until the wood acidity of product B reaches 6.5 to obtain product B.
[0028] c. Soak product B in running water for 4 days to obtain product C1; air-dry product C1 so that the moisture content of product C1 is 12% to obtain product C.
[0029] d. Put product C into a steam box to heat for 3 hours, and keep the water content of product C at 15% by adjusting the steam saturation in the steam box to obtain product D.
[0030] e. Put product D into a mold for straightening, and heat product D while straightening, so that the moisture content of product D is 8%, to obtain product E1; product E1 is cooled at room temperature, and left to stand for 5 hours to obtain a finished product.
Embodiment 3
[0031] Example 3. A kind of energy-saving mahogany straightening process, comprises the following steps,
[0032] a, soak the mahogany in the form of wooden squares with 30% hydrochloric acid solution for 80 hours to get product A,
[0033] b. Soak product A with ammonia water until the wood acidity of product B reaches 7 to obtain product B.
[0034] c. Soak product B in running water for 2 days to obtain product C1; air-dry product C1 so that the moisture content of product C1 is 18%, and obtain product C.
[0035] d. Put product C into a steam box to heat for 2 hours, and keep the moisture content of product C at 20% by adjusting the steam saturation in the steam box to obtain product D.
[0036] e. Put product D into a mold for straightening, and heat product D while straightening, so that the moisture content of product D is 12%, to obtain product E1; product E1 is cooled at room temperature, and left to stand for 3 hours to obtain a finished product.
[0037] The inve...
PUM
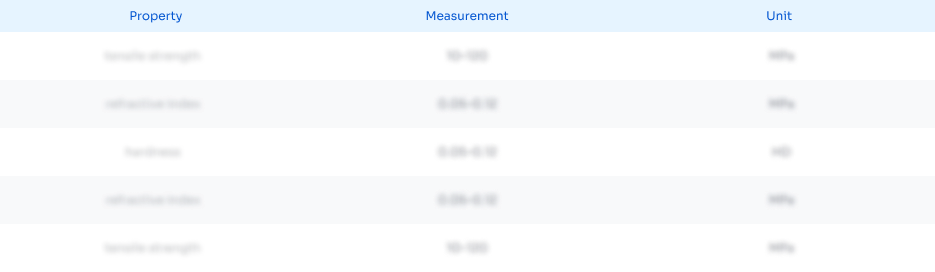
Abstract
Description
Claims
Application Information

- R&D
- Intellectual Property
- Life Sciences
- Materials
- Tech Scout
- Unparalleled Data Quality
- Higher Quality Content
- 60% Fewer Hallucinations
Browse by: Latest US Patents, China's latest patents, Technical Efficacy Thesaurus, Application Domain, Technology Topic, Popular Technical Reports.
© 2025 PatSnap. All rights reserved.Legal|Privacy policy|Modern Slavery Act Transparency Statement|Sitemap|About US| Contact US: help@patsnap.com