Unmanned aerial vehicle inspection system and inspection method
An inspection system and unmanned aerial vehicle technology, applied in the field of inspection, can solve the problems of poor ability of independent judgment, affecting inspection efficiency, and low inspection accuracy
- Summary
- Abstract
- Description
- Claims
- Application Information
AI Technical Summary
Problems solved by technology
Method used
Image
Examples
Embodiment 1
[0043] figure 1 It is a schematic structural diagram of an unmanned aerial vehicle inspection system provided by Embodiment 1 of the present invention. This embodiment can be applied to the field of inspection of poles and towers in the power grid. figure 1 , The drone inspection system includes: the drone 10, a control unit 20, at least one first vehicle-mounted platform 30 and at least one second vehicle-mounted platform 40; wherein the control unit 20 is communicatively connected with the drone 10 for According to the inspection task, the drone 10 is controlled to work, and the image signals collected by the drone 10 are received; the first vehicle-mounted platform 30 is provided with a control unit 20, and the first vehicle-mounted platform 30 is movable and provides for the drone 10 The first platform for the man-machine 10 to lift; the second vehicle-mounted platform 40 is provided with a control unit 20, and the second vehicle-mounted platform 40 is movable and provides th...
Embodiment 2
[0047] figure 2 It is a schematic structural diagram of a hangar provided in the second embodiment of the present invention. On the basis of the first embodiment, refer to figure 2 Optionally, both the first vehicle-mounted platform and the second vehicle-mounted platform include a hangar 50 and a mobile vehicle body. The hangar 50 is located on the mobile vehicle body. The drone can land on the hangar 50 and rise in the hangar 50 Up.
[0048] Among them, the UAV 10 rises from the hangar 50 when it starts the inspection task, and after completing the inspection task, it lands to the hangar 50, and the first vehicle platform and the second vehicle platform can be moved by their respective mobile bodies, correspondingly The hangar 50 on the mobile vehicle body can move with the corresponding vehicle-mounted platform to move to the target location to facilitate the take-off and landing of the drone 10.
[0049] Optionally, the hangar 50 is provided with a rolling shutter door 51, a ...
Embodiment 3
[0059] image 3 It is a flowchart of a drone inspection method provided in the third embodiment of the present invention. The method can be executed by the drone inspection system described in the foregoing embodiment, and specifically includes the following steps:
[0060] Step 110: The control unit generates a control signal according to the inspection task.
[0061] Among them, the control unit can send control instructions to the drone to control the working status of the drone. The inspection task can be an inspection task instruction input to the control unit according to the actual inspection task requirements, and the control signal can be to control the drone. The signal for the drone to perform the inspection task. When the drone is required to inspect the power line, the control unit generates a control signal according to the inspection task and sends the control signal to the drone.
[0062] Step 120: The drone is raised on the first vehicle-mounted platform according to...
PUM
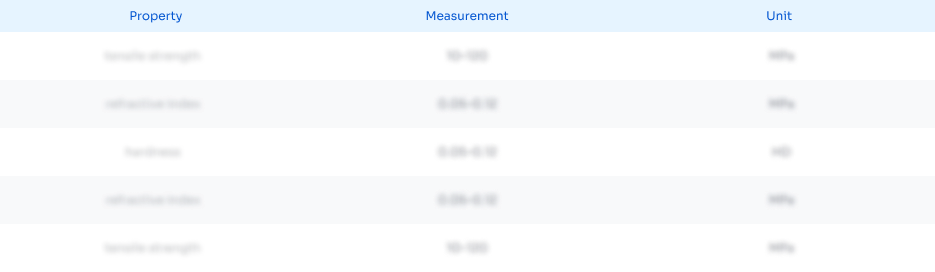
Abstract
Description
Claims
Application Information

- R&D Engineer
- R&D Manager
- IP Professional
- Industry Leading Data Capabilities
- Powerful AI technology
- Patent DNA Extraction
Browse by: Latest US Patents, China's latest patents, Technical Efficacy Thesaurus, Application Domain, Technology Topic, Popular Technical Reports.
© 2024 PatSnap. All rights reserved.Legal|Privacy policy|Modern Slavery Act Transparency Statement|Sitemap|About US| Contact US: help@patsnap.com