Technical method for stably reducing coal consumption of cement clinker firing
A technology of cement clinker and coal consumption, applied in cement production, etc., can solve the problem of high coal consumption, achieve the effects of reducing production costs, significant economic benefits, and reducing process technology
- Summary
- Abstract
- Description
- Claims
- Application Information
AI Technical Summary
Problems solved by technology
Method used
Image
Examples
Embodiment 1
[0019] see figure 1 , the present invention provides a technical method for stably reducing the coal consumption of cement clinker firing. Medium silica rock and silica with good burnability are used to replace high silica rock with poor grindability and burnability; industrial waste yellow phosphorus slag is mixed as mineralizer; fly ash is used to improve the burnability of raw meal.
[0020] 1) Conduct a full chemical analysis of all raw material components in raw meal ingredients. The main raw materials are: limestone, high silica rock, medium silica rock, silica, yellow phosphorus slag, converter slag, fly ash, etc.
[0021] 2) Design ideas: Use medium silica rock and silica with better combustibility to replace high silica rock with poor combustibility, mix industrial waste yellow phosphorus slag as mineralizer, and design different raw material formulas to verify the combustibility of raw materials.
[0022] Table 2-1 Chemical Composition of Raw Materials (%)
[0023...
Embodiment 2
[0035] see figure 1 , the present invention provides a technical method for stably reducing the coal consumption of cement clinker firing. Recovery efficiency; optimize the structure of the grate plate and the control of the grate cooler to improve the efficiency of heat recovery; expand the diameter of the air supply pipe of the inflatable beam to increase the air volume and improve the efficiency of heat recovery.
[0036] Table 3-1 Optimization of Fan Configuration of Grate Cooler
[0037]
[0038]
[0039] Expand the diameter of the connecting pipe between the fan and the inflatable beam pipe from the original Ф108㎜ to Ф168㎜, and eliminate the turbulent flow area of the bellows, so as to reduce the pipe resistance and increase the air volume.
Embodiment 3
[0041] see figure 1 , the present invention provides a technical method for stably reducing the coal consumption of cement clinker firing. Oxygen content at the outlet of device C1; use a new flap valve to reduce internal air leakage, and the sealing device at the kiln tail is transformed from a cylinder seal to a graphite seal to reduce external air leakage; use a new type of spreading box to increase the dispersion of materials in the calciner and preheater, thereby improving Heat exchange efficiency; optimize the position of the furnace coal burner, use a new structure of the furnace coal burner, and improve the combustion efficiency and burnout rate of pulverized coal.
[0042] After optimization, the secondary air temperature is stable at 1200±25°C, and the tertiary air temperature is stable at 1050±20°C. The level of the secondary air temperature and the tertiary air temperature is a key indicator parameter reflecting the heat recovery efficiency of the system. Through...
PUM
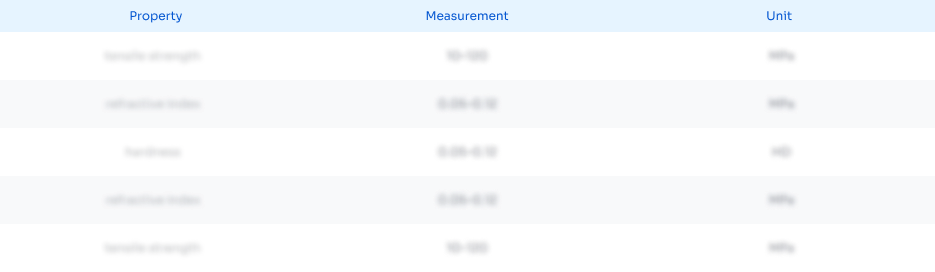
Abstract
Description
Claims
Application Information

- Generate Ideas
- Intellectual Property
- Life Sciences
- Materials
- Tech Scout
- Unparalleled Data Quality
- Higher Quality Content
- 60% Fewer Hallucinations
Browse by: Latest US Patents, China's latest patents, Technical Efficacy Thesaurus, Application Domain, Technology Topic, Popular Technical Reports.
© 2025 PatSnap. All rights reserved.Legal|Privacy policy|Modern Slavery Act Transparency Statement|Sitemap|About US| Contact US: help@patsnap.com