Robot joint device
A technology of robot joints and connecting rods, applied in transmission devices, gear transmission devices, manipulators, etc., can solve the problems of reduced durability, limited steering range of motion, and difficulty in precise control, and achieve improved durability, high strength and rigidity. , Improve the effect of precise control
- Summary
- Abstract
- Description
- Claims
- Application Information
AI Technical Summary
Problems solved by technology
Method used
Image
Examples
Embodiment Construction
[0045] A robot joint device according to an embodiment of the present invention includes: a first plate and a second plate arranged parallel to each other; a connecting rod connected to the first plate at one end and connected to the second plate at the other end; a connecting member , respectively connected to the two ends of the connecting rod and the first plate and the second plate, so that the connecting rod can adjust the angle and rotation of the first plate and the second plate; the rotating shaft, the two ends are respectively through the first plate and the second plate, and rotatably arranged; the gear reduction part is arranged inside the first plate and connected to one end of the rotating shaft; the pulley is connected to the end of the rotating shaft The other end transmits the driving force to the rotating shaft; and the driving part transmits the driving force to the pulley, the connecting rod is composed of a plurality of one ends and the other ends respective...
PUM
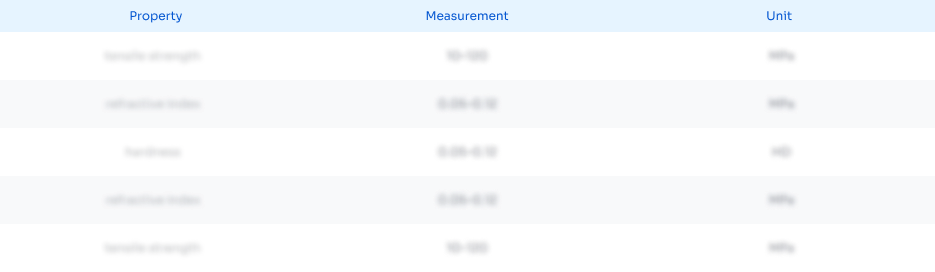
Abstract
Description
Claims
Application Information

- R&D Engineer
- R&D Manager
- IP Professional
- Industry Leading Data Capabilities
- Powerful AI technology
- Patent DNA Extraction
Browse by: Latest US Patents, China's latest patents, Technical Efficacy Thesaurus, Application Domain, Technology Topic, Popular Technical Reports.
© 2024 PatSnap. All rights reserved.Legal|Privacy policy|Modern Slavery Act Transparency Statement|Sitemap|About US| Contact US: help@patsnap.com