Broaching machining stability monitoring method and system
A technology of stability and stability graph, which is applied in metal processing equipment, metal processing machinery parts, broaching machines, etc., can solve the relative position deviation between the tool and the workpiece, and achieve the effect of solving the relative position deviation
- Summary
- Abstract
- Description
- Claims
- Application Information
AI Technical Summary
Problems solved by technology
Method used
Image
Examples
Embodiment 1
[0038] Such as figure 1 As shown, the invention discloses a method for monitoring the stability of broaching, comprising the following steps:
[0039] Collect multiple sets of time-domain signals of the vibration of the broaching machine tool and the workpiece installed on it when working at the broaching speed to be monitored, and extract the drive frequency of the machine tool and the transmission chain from the multiple sets of time-domain signals. vibration frequency and random frequency;
[0040] Through the modal test, the different modal parameters of the broaching machine tool when working at the drive frequency of the machine tool, the vibration frequency of the transmission chain and the random frequency are obtained; the processing stability diagram of the broaching machine tool is constructed under different modal parameters, Then constructing an acceleration stability diagram of the broaching machine tool according to the processing stability diagram;
[0041] A...
Embodiment 2
[0045]Embodiment 2 is a preferred embodiment of Embodiment 1. It differs from Embodiment 1 in that the specific steps of the broaching stability monitoring method are refined and optimized, specifically including the following:
[0046] Machine tools are ubiquitous and difficult to avoid vibration, which mainly includes the vibration generated by the idling of the machine tool and the vibration during the cutting process. Among the above vibrations, there are free vibration, forced vibration, self-excited vibration and mixed vibration. Since the vibration of various structures in precision broaching affects the precision of processing, and the vibration of its structure corresponds to its dynamic characteristics, in order to solve this problem, the broaching stability monitoring method and system provided in this embodiment, Obtain the vibration frequency of the vibration source and the corresponding modal parameters (modal stiffness, modal mass) through the modal test, and es...
PUM
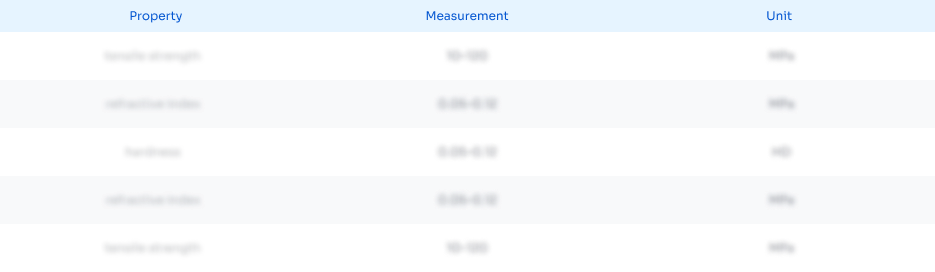
Abstract
Description
Claims
Application Information

- R&D
- Intellectual Property
- Life Sciences
- Materials
- Tech Scout
- Unparalleled Data Quality
- Higher Quality Content
- 60% Fewer Hallucinations
Browse by: Latest US Patents, China's latest patents, Technical Efficacy Thesaurus, Application Domain, Technology Topic, Popular Technical Reports.
© 2025 PatSnap. All rights reserved.Legal|Privacy policy|Modern Slavery Act Transparency Statement|Sitemap|About US| Contact US: help@patsnap.com