Assembling and welding manufacturing process of large pressure vessel
A pressure vessel and manufacturing process technology, which is applied in the field of large-scale pressure vessel assembly and welding manufacturing process, can solve the problems of position deviation, end cap offset, and heavy weight after welding of end caps, so as to avoid position deviation, improve accuracy, and improve quality effect
- Summary
- Abstract
- Description
- Claims
- Application Information
AI Technical Summary
Problems solved by technology
Method used
Image
Examples
Embodiment Construction
[0037] The embodiments of the present invention are described in detail below with reference to the accompanying drawings, but the present invention can be implemented in many different ways as defined and covered by the claims.
[0038] like Figure 1 to Figure 8 As shown, this embodiment provides a large-scale pressure vessel assembly and welding manufacturing machine, including a horizontally arranged bottom plate 1, a turntable 2 is installed horizontally on the upper surface of the bottom plate 1, and a base 3 is fixedly installed on the upper surface of the turntable 2. The upper surface of the base 3 is provided with an annular groove 4 which cooperates with the cylinder of the pressure vessel. The upper surface of the base 3 is located at the center of the annular groove 4 and is vertically and fixedly connected with a mounting column 5 .
[0039] A sliding slot 6 is vertically opened on the mounting column 5 , and an electric sliding sleeve 7 matched with the outer s...
PUM
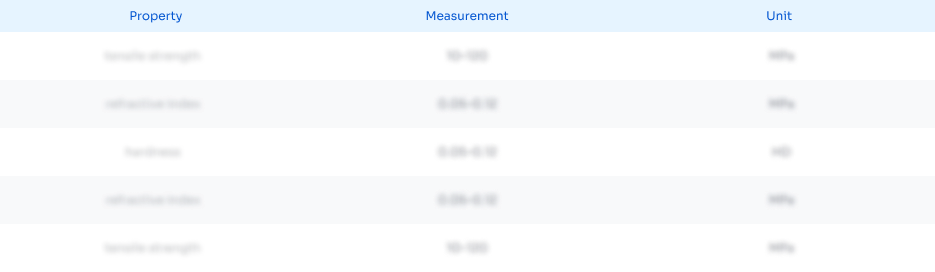
Abstract
Description
Claims
Application Information

- Generate Ideas
- Intellectual Property
- Life Sciences
- Materials
- Tech Scout
- Unparalleled Data Quality
- Higher Quality Content
- 60% Fewer Hallucinations
Browse by: Latest US Patents, China's latest patents, Technical Efficacy Thesaurus, Application Domain, Technology Topic, Popular Technical Reports.
© 2025 PatSnap. All rights reserved.Legal|Privacy policy|Modern Slavery Act Transparency Statement|Sitemap|About US| Contact US: help@patsnap.com