Self-balancing lifting device and control method thereof
A technology of lifting device and control method, which is applied in the direction of lifting equipment, transportation and packaging in mines, can solve the problems of limitation, large space occupation, overweight, etc., and achieve high feasibility, low power demand and small space occupation Effect
- Summary
- Abstract
- Description
- Claims
- Application Information
AI Technical Summary
Problems solved by technology
Method used
Image
Examples
Embodiment Construction
[0039]The present invention is a self-balancing lifting device and its control method, which includes a counterweight 1, a load box 2, and a rotating traction mechanism between the two. The rotating traction mechanism includes a rotating shaft 3 and a Traction mechanism, the traction mechanism includes a rotating disk 4, a telescopic device 5 and a traction rope 6 on the outside thereof; Above, the two ends of the traction rope 6 are respectively connected with the counterweight 1 and the load box 2; the top of the telescopic device is provided with a slot 7, and the traction rope 4 passes through the slot 7; the rotation The shaft 3 is connected to the electric motor or the hydraulic motor, the gravity sensor 8 is arranged at the connection between the traction rope 6 and the counterweight 1 and the load box 2, and the signal output end of the gravity sensor 8 is connected to the controller, and the The controller controls the telescopic length of the telescopic device 5; the...
PUM
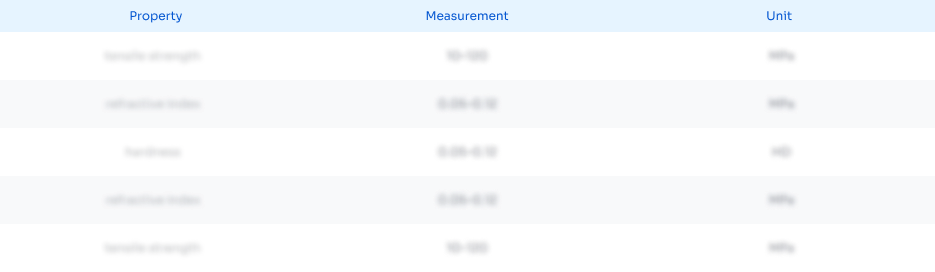
Abstract
Description
Claims
Application Information

- R&D
- Intellectual Property
- Life Sciences
- Materials
- Tech Scout
- Unparalleled Data Quality
- Higher Quality Content
- 60% Fewer Hallucinations
Browse by: Latest US Patents, China's latest patents, Technical Efficacy Thesaurus, Application Domain, Technology Topic, Popular Technical Reports.
© 2025 PatSnap. All rights reserved.Legal|Privacy policy|Modern Slavery Act Transparency Statement|Sitemap|About US| Contact US: help@patsnap.com