Preparation method of a superhydrophobic strain sensor composite material
A strain sensor and composite material technology, which is applied in the field of superhydrophobic composite material preparation, can solve the problem of few superhydrophobic stretchable sensors, and achieve the effect of maintaining sensitivity, good mechanical strength and thermal stability, and excellent sensitivity
- Summary
- Abstract
- Description
- Claims
- Application Information
AI Technical Summary
Problems solved by technology
Method used
Image
Examples
Embodiment 1
[0025] A preparation method of a superhydrophobic strain sensor composite material is carried out according to the following steps:
[0026] (1) Dissolve 0.3g of heptafluorobutyric acid in 3g of tetrahydrofuran and stir for 1h, then add 0.5g of tetraethoxysilane and stir for 3h, put the mixed solution in an evaporating dish and dry it naturally to obtain fluorinated solidified agent;
[0027] (2) Dissolve 0.2g of perfluorooctyltriethoxysilane in 10g of dimethylformamide, and stir the solution for 2h, then add 0.2g of carbon nanotubes, in order to ensure uniformity, the The solution was sonicated for 30 minutes, and magnetically stirred for 6 hours, then the carbon nanotube-based solution was poured into an evaporating dish, and after natural air drying, the hydrophobic carbon nanotube powder was synthesized and collected;
[0028] (3) Disperse 0.3 g of carbon nanofibers for polymer toughening in 5 g of tetrahydrofuran, then add 5 g of polydimethylsiloxane and stir for 2 h and...
Embodiment 2
[0033] A preparation method of a superhydrophobic strain sensor composite material is carried out according to the following steps:
[0034] (1) Dissolve 0.3g of heptafluorobutyric acid in 3.5g of tetrahydrofuran and stir for 1.2h, then add 0.5g of tetraethoxysilane and stir for 3h, put the mixed solution in an evaporating dish and dry it naturally to obtain fluorine curing agent;
[0035] (2) Dissolve 0.2g of perfluorooctyltriethoxysilane in 12g of dimethylformamide, and stir the solution for 1.8h, then add 0.2g of carbon nanotubes, in order to ensure uniformity, the The tube solution was sonicated for 30 minutes, and magnetically stirred for 6 hours, then the carbon nanotube-based solution was poured into an evaporating dish, and after natural air-drying, the hydrophobic carbon nanotube powder was synthesized and collected;
[0036] (3) Disperse 0.3 g of carbon nanofibers for polymer toughening in 6 g of tetrahydrofuran, then add 5 g of polydimethylsiloxane and stir for 2 h...
Embodiment 3
[0041] A preparation method of a superhydrophobic strain sensor composite material is carried out according to the following steps:
[0042] (1) Dissolve 0.25g of heptafluorobutyric acid in 3g of tetrahydrofuran and stir for 0.9h, then add 0.5g of tetraethoxysilane and stir for 3h, put the mixed solution in an evaporating dish and dry it naturally to obtain fluorinated Hardener;
[0043](2) Dissolve 0.25g of perfluorooctyltriethoxysilane in 12g of dimethylformamide, and stir the solution for 2.5h, then add 0.25g of carbon nanotubes, in order to ensure uniformity, the The tube solution was sonicated for 30 minutes, and magnetically stirred for 5 hours, then the carbon nanotube-based solution was poured into an evaporating dish, and after natural air drying, the hydrophobic carbon nanotube powder was synthesized and collected;
[0044] (3) Disperse 0.3g of carbon nanofibers for polymer toughening in 6g of tetrahydrofuran, then add 6g of polydimethylsiloxane and stir for 2.5h an...
PUM
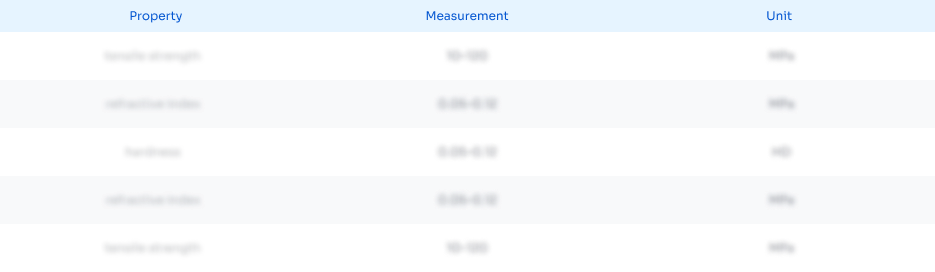
Abstract
Description
Claims
Application Information

- R&D
- Intellectual Property
- Life Sciences
- Materials
- Tech Scout
- Unparalleled Data Quality
- Higher Quality Content
- 60% Fewer Hallucinations
Browse by: Latest US Patents, China's latest patents, Technical Efficacy Thesaurus, Application Domain, Technology Topic, Popular Technical Reports.
© 2025 PatSnap. All rights reserved.Legal|Privacy policy|Modern Slavery Act Transparency Statement|Sitemap|About US| Contact US: help@patsnap.com