Boiler economizer pipeline manufacturing, machining and forming method
An economizer pipe, processing and forming technology, applied in the direction of manufacturing tools, chemical instruments and methods, metal processing equipment, etc., can solve the problems of pipeline impurities, affecting the welding effect, long storage time of pipelines, etc., and achieve the goal of ensuring continuity Effect
- Summary
- Abstract
- Description
- Claims
- Application Information
AI Technical Summary
Problems solved by technology
Method used
Image
Examples
Embodiment Construction
[0033] In order to make the technical problems, technical solutions and beneficial effects to be solved by the present invention clearer, the present invention will be further described in detail below in conjunction with the accompanying drawings and embodiments. It should be understood that the specific embodiments described here are only used to explain the present invention, not to limit the present invention.
[0034] Refer to 1-9, a boiler economizer pipeline manufacturing processing molding method, which uses a boiler economizer pipeline manufacturing processing molding device, the boiler economizer pipeline manufacturing processing molding device includes a support table 1. The supporting plate 2, the cleaning mechanism 3, the conveying mechanism 4, the placing plate 5, the support roller 6 and the positioning and fixing mechanism 7, when using the above-mentioned boiler economizer pipeline manufacturing processing forming device to weld the pipe and fin Methods as bel...
PUM
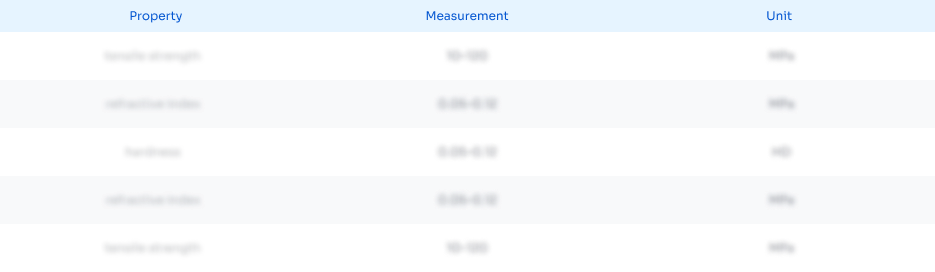
Abstract
Description
Claims
Application Information

- R&D
- Intellectual Property
- Life Sciences
- Materials
- Tech Scout
- Unparalleled Data Quality
- Higher Quality Content
- 60% Fewer Hallucinations
Browse by: Latest US Patents, China's latest patents, Technical Efficacy Thesaurus, Application Domain, Technology Topic, Popular Technical Reports.
© 2025 PatSnap. All rights reserved.Legal|Privacy policy|Modern Slavery Act Transparency Statement|Sitemap|About US| Contact US: help@patsnap.com