Fabric color printing process
A printing process and color technology, applied in printing, printing machines, rotary printing machines, etc., can solve the problems of overlapping printing, affecting the elasticity of T-shirts, and affecting printing quality, etc., to achieve fast output at the output end, high printing effect, and avoid wrinkles The effect of uplift
- Summary
- Abstract
- Description
- Claims
- Application Information
AI Technical Summary
Problems solved by technology
Method used
Image
Examples
Embodiment 1
[0086] Such as figure 1 Shown, a kind of fabric color printing process comprises:
[0087] Step 1: The cloth is unfolded. First, the cloth 10 is manually placed on the cloth receiving plate 2 at the input end, and then the drive assembly 41 is started to move vertically upward. The drive assembly 41 drives the buckle unit 31 to lift up, and then the drive shaft 412 drives Go to the bottom of the cloth piece 10, and gradually push up the cloth piece 10, at this time, start the control assembly 44 to move vertically upwards, the struts a431 are flattened and are all located on the same horizontal plane, and the cloth piece 10 completes the unfolding work;
[0088] Step 2: Flatten the cloth. After the cloth 10 is flattened, the driving assembly 41 is reset. During the reset process, the transmission assembly 46 synchronously drives the compacting assembly 45 to descend, and then the cloth 10 falls onto the cloth connecting plate 2. Simultaneously, the flattening of the cloth blo...
Embodiment 2
[0103] Such as Figure 4 , figure 2 and image 3 As shown, a T-shirt processing garment fabric color printing machine includes a printing machine 1 and several groups of cloth connecting plates 2 arranged at equal intervals along the transmission direction of the printing machine 1, and also includes a lapping plate arranged on the cloth connecting plate 2 Button mechanism 3, a flattening mechanism 4 arranged at the input end of the printing machine 1, a printing mechanism 5 arranged behind the flattening mechanism 4, and a drying mechanism 6 arranged behind the printing mechanism 5;
[0104] The printing machine 1 is sequentially provided with an input station 11, a printing station 12 and a drying station 13 along its transmission direction, the flattening mechanism 4 is located at the flattening mechanism 4, and the printing mechanism 5 is located at the printing mechanism 5 and The drying mechanism 6 is located at the drying station 13;
[0105] The bottom of the print...
Embodiment 3
[0150] Such as Figure 25 , Figure 23 and Figure 24 As shown, the parts that are the same as or corresponding to those in the second embodiment adopt the reference numerals corresponding to the second embodiment. For the sake of simplicity, only the differences from the second embodiment are described below. The difference between this embodiment three and embodiment two is:
[0151] further, such as Figure 25 , Figure 23 and Figure 24 As shown, the pressing assembly 47 includes a frame 451, a telescopic unit 452 arranged on the frame 451 and arranged vertically downward, a support rod 453 fixedly connected to the lower end of the telescopic unit 452 and connected to the The lower end of the support rod 453 is fixedly connected to the pressing plate 454, and the support rod 453 is slidingly arranged in the T-shaped groove 457 of the frame 451 through the T-shaped rod 456;
[0152] The transmission assembly 46 includes a one-way rack 461 fixedly connected to the driv...
PUM
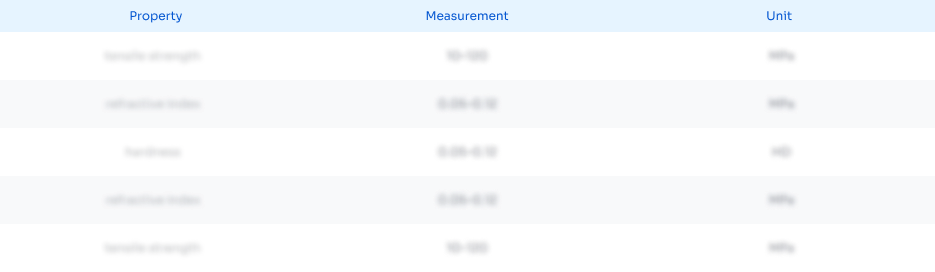
Abstract
Description
Claims
Application Information

- R&D
- Intellectual Property
- Life Sciences
- Materials
- Tech Scout
- Unparalleled Data Quality
- Higher Quality Content
- 60% Fewer Hallucinations
Browse by: Latest US Patents, China's latest patents, Technical Efficacy Thesaurus, Application Domain, Technology Topic, Popular Technical Reports.
© 2025 PatSnap. All rights reserved.Legal|Privacy policy|Modern Slavery Act Transparency Statement|Sitemap|About US| Contact US: help@patsnap.com