Framed plate for electronic equipment and plastic forming method
An electronic equipment, plastic molding technology, applied in the direction of electrical equipment shell/cabinet/drawer, electrical components, chassis/cabinet/drawer parts, etc., can solve the problems of large shrinkage, sheet deformation, etc. The effect of plastic usage, enhancement of mechanical strength, and reduction of sheet deformation
- Summary
- Abstract
- Description
- Claims
- Application Information
AI Technical Summary
Problems solved by technology
Method used
Image
Examples
Embodiment 1
[0031] The embodiment of the present invention provides a framed board for electronic equipment, please refer to the attached Figure 1-2 , used to make housings for electronic devices, the framed sheet includes:
[0032] board body 1;
[0033] Specifically, the board body 1 is a board with a certain shape and a certain shape, and a plurality of the board bodies 1 are assembled together to form a casing, and electronic equipment is arranged in the casing.
[0034] A frame body 2, the frame body 2 is fixed on the edge of the upper surface of the board body 1;
[0035] Further, the frame body includes: a third surface, the third surface is fixed on the upper surface of the board body 1 by pasting to form an overlapping portion, the width of the overlapping portion is K, and the third surface The width of the surface is P; where, 0.5P≤K≤P.
[0036] Specifically, the panel body 1 has an upper surface, a lower surface and side edges, and the upper surface and the lower surface a...
Embodiment 2
[0068] The present application also provides a plastic molding method for making the framed sheet for electronic equipment, please refer to the attached Figure 1-2 , the plastic molding method includes:
[0069] Step 1: paste the frame body 2 on the edge of the upper surface of the board body 1;
[0070] Step 2: Put the board body 1 with the frame body 2 fixed into the mold;
[0071] Step 3: pouring plastic material into the mold to form the first plastic body 9 and the second plastic body 10;
[0072] Step 4: After the plastic material is solidified, remove the mold.
[0073] Further, the mold has at least two injection ports.
[0074] Specifically, the mold includes at least two injection ports, namely a first injection port and a second injection port, and plastic material is poured into the first injection port to form the first plastic body 9; Plastic material is poured into the second injection port to form the second plastic body 10 .
[0075] Through the plastic ...
PUM
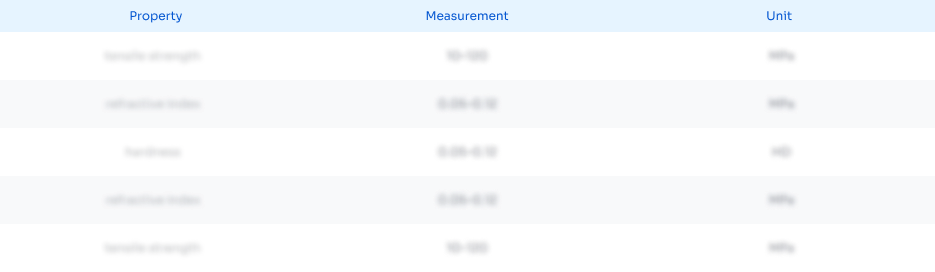
Abstract
Description
Claims
Application Information

- R&D Engineer
- R&D Manager
- IP Professional
- Industry Leading Data Capabilities
- Powerful AI technology
- Patent DNA Extraction
Browse by: Latest US Patents, China's latest patents, Technical Efficacy Thesaurus, Application Domain, Technology Topic, Popular Technical Reports.
© 2024 PatSnap. All rights reserved.Legal|Privacy policy|Modern Slavery Act Transparency Statement|Sitemap|About US| Contact US: help@patsnap.com