Closed-loop control method and system based on power pulse width driving
A closed-loop control and closed-loop technology, applied in electric controllers, controllers with specific characteristics, etc., can solve problems such as low energy efficiency, complex PID application, and difficulty in optimal system setting, achieving automatic control and maximum energy efficiency. the effect of
- Summary
- Abstract
- Description
- Claims
- Application Information
AI Technical Summary
Problems solved by technology
Method used
Image
Examples
Embodiment 1
[0036] See figure 1 , which shows a flow chart of a closed-loop control method based on power pulse width drive for a multi-task, multi-objective closed-loop control system, the closed-loop control method includes the following steps:
[0037] Step 101, each controller pre-stores setting parameters that enable the corresponding controlled object to be in the required operating state, and the controller controls the corresponding driving object to implement driving, so that the corresponding controlled object is in the state corresponding to the setting parameters. operating status;
[0038] Step 102, setting each controller and its corresponding controlled power pulse width drive object and corresponding adjusted feedback parameters as a separate closed-loop block; wherein, the setting parameters include the final target setting corresponding to the final target feedback parameter parameter;
[0039] Step 103, the controllers in each closed-loop block detect the real-time fe...
Embodiment 2
[0046] See image 3 , which shows a system structure diagram of a multi-heat source, multi-task, multi-objective closed-loop control system, each controller is pre-stored with setting parameters that can make the corresponding controlled object in the required operating state, a single controller, and It controls the driving object of the real-time feedback parameter corresponding to the setting parameter, which is set as a separate closed-loop block; the setting parameter includes the final target setting parameter corresponding to the final target feedback parameter, and the real-time feedback parameter can be passed, as shown in the figure The solid line arrow refers to the direction of water flow, that is, devices such as valves and pumps adjust the controlled objects such as hot water tanks, constant temperature water tanks, etc., and the dotted line arrows refer to the driving objects, that is, the ignition device or flameout The adjustment of the device to the controlle...
PUM
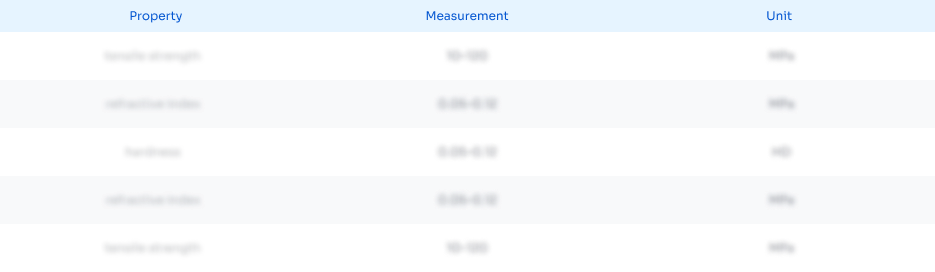
Abstract
Description
Claims
Application Information

- R&D
- Intellectual Property
- Life Sciences
- Materials
- Tech Scout
- Unparalleled Data Quality
- Higher Quality Content
- 60% Fewer Hallucinations
Browse by: Latest US Patents, China's latest patents, Technical Efficacy Thesaurus, Application Domain, Technology Topic, Popular Technical Reports.
© 2025 PatSnap. All rights reserved.Legal|Privacy policy|Modern Slavery Act Transparency Statement|Sitemap|About US| Contact US: help@patsnap.com