Lifting system with three-direction motion compensation function
A functional, mobile trolley technology, applied in the field of lifting systems, can solve the problems of low lifting efficiency, long-term filling and drainage, complex structure, etc., and achieve the effects of high lifting efficiency, low comprehensive cost, and balanced force
- Summary
- Abstract
- Description
- Claims
- Application Information
AI Technical Summary
Problems solved by technology
Method used
Image
Examples
Embodiment Construction
[0035] The following will clearly and completely describe the technical solutions in the embodiments of the present invention with reference to the accompanying drawings in the embodiments of the present invention. Obviously, the described embodiments are only some, not all, embodiments of the present invention. Based on the embodiments of the present invention, all other embodiments obtained by persons of ordinary skill in the art without making creative efforts belong to the protection scope of the present invention.
[0036] like figure 1 As shown, the lifting system with the three-way motion compensation function of the present invention includes the main arm 1, the moving trolley I5, the moving trolley II2, the support II3, the support I4, the lifting mechanism 6 and the hull 7. The front end of the main arm 1 is installed on the upper end of the mobile trolley I5, the rear end of the main arm 1 is installed on the upper end of the mobile trolley II2, the lower end of the...
PUM
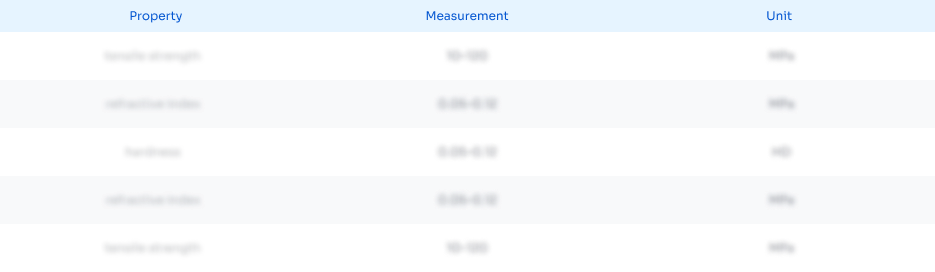
Abstract
Description
Claims
Application Information

- R&D Engineer
- R&D Manager
- IP Professional
- Industry Leading Data Capabilities
- Powerful AI technology
- Patent DNA Extraction
Browse by: Latest US Patents, China's latest patents, Technical Efficacy Thesaurus, Application Domain, Technology Topic, Popular Technical Reports.
© 2024 PatSnap. All rights reserved.Legal|Privacy policy|Modern Slavery Act Transparency Statement|Sitemap|About US| Contact US: help@patsnap.com