Large-span bridge multi-point deflection measurement method considering camera attitude change
A camera attitude and deflection measurement technology, which is applied in the testing of machines/structural components, measuring devices, elastic testing, etc., can solve problems such as the decline in displacement extraction accuracy, unsatisfactory image focus, and unsuccessful template matching, etc., to achieve visual saving. Accurate and convenient field and scale calibration, and improved work efficiency
- Summary
- Abstract
- Description
- Claims
- Application Information
AI Technical Summary
Problems solved by technology
Method used
Image
Examples
Embodiment 1
[0104] In order to verify the reliability of the deformation measurement method based on camera attitude correction proposed in this patent, a displacement platform test was carried out on the vibration isolation optical test bench. In the experimental site shown in the figure below, a UI-3370CP-M industrial camera with a resolution of 2048pixel×2048pixel and a pixel size of 5.5μm is equipped with a Kowa lens with f=25mm. This optical system is installed in a precision electronically controlled displacement The stage can provide the camera with three aspects of attitude changes: pitch, rotation around the optical axis, and in-plane rigid body displacement. The camera is clearly focused on the stable speckle area and is guaranteed to be in the same window as the target. After taking the first reference picture, the target surface is made to settle by 5mm (true value) through the translation stage, and a certain small attitude change is randomly made for the camera. Collect 100...
Embodiment 2
[0114] This patent uses the proposed optical measurement method to measure the deflection of multiple sections in a static load test of a long-span bridge. Stiffening beam deflection measuring points are arranged in the mid-span L / 2 (C measuring point), 3L / 8 (M1 measuring point), L / 4 (M2 measuring point), L / 8 (M3 measuring point) near the section. The test vehicle is planned to be a test truck with a total weight of 350kN. 64 trucks are loaded in four stages. like Figure 4 shown.
[0115] Step 1: Determine the layout of the optical collection system
[0116] as above Figure 5 As shown, the IDS industrial camera is equipped with f=200mm telephoto fixed-focus lens, and is erected on the inspection road across the section, with the structural surface at the bottom of the Canton Tower as a stable area. The camera is set up on the inspection road downstream of the mid-span section, with the line of sight facing the direction of the Guangdong Tower. like Image 6 As shown, ...
PUM
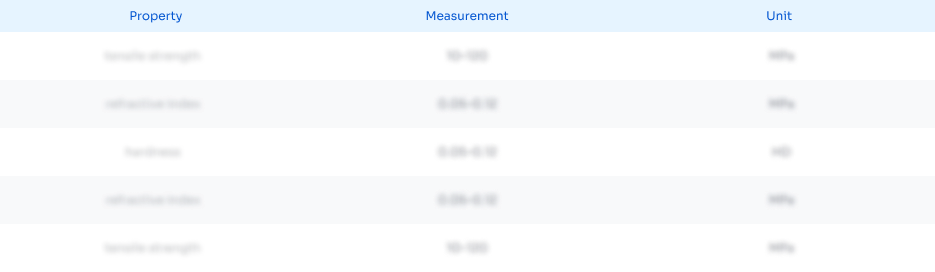
Abstract
Description
Claims
Application Information

- R&D
- Intellectual Property
- Life Sciences
- Materials
- Tech Scout
- Unparalleled Data Quality
- Higher Quality Content
- 60% Fewer Hallucinations
Browse by: Latest US Patents, China's latest patents, Technical Efficacy Thesaurus, Application Domain, Technology Topic, Popular Technical Reports.
© 2025 PatSnap. All rights reserved.Legal|Privacy policy|Modern Slavery Act Transparency Statement|Sitemap|About US| Contact US: help@patsnap.com