Driving device for optical inspection outside material cabin and exposure platform
A technology of driving device and installation platform, applied in the direction of lifting device, analyzing material, measuring device, etc., can solve the problems that the driving mechanism cannot adapt to the space environment, safety and reliability cannot meet the space station, etc., to achieve all-round monitoring, satisfaction Safety and reliability, the effect of high safety and reliability
- Summary
- Abstract
- Description
- Claims
- Application Information
AI Technical Summary
Problems solved by technology
Method used
Image
Examples
Embodiment 1
[0078] Such as Figure 1-Figure 9 As shown, a driving device for optical inspection of materials outside the cabin in this embodiment includes:
[0079] The track 801 for the steel belt 802 to move; the steel belt is the transmission actuator, which utilizes the steel belt's own rigidity to drive the steel belt to reciprocate linearly in a limited space under the drive of the steel belt friction wheel;
[0080] The driving friction wheel 803 is connected with the driving mechanism 804 and rotates under the driving of the driving mechanism 804; the driving mechanism 804 can be selected from a driving motor; the driving friction wheel is a steel belt clamping device, which forms a normal direction on the steel belt by clamping Compression force, providing support for friction drive;
[0081] The driving friction wheel 805 is arranged side by side with the driving friction wheel 804 at intervals, and is located on both sides of the track 801 respectively, and the steel belt 802 ...
Embodiment 2
[0115] A material exposed platform outside the cabin of this embodiment, such as Figure 1-Figure 9 As shown, it includes a test box, an optical inspection module, an installation platform 820 and the drive device described in Embodiment 1, the test box is installed on the installation platform 820, and the exposed surface of the test box after opening faces the installation The surroundings of the platform 820 are arranged, and the track 801 is arranged at a position close to the peripheral side of the installation platform 820; the bottom of the bracket 701 is provided with a connecting plate 714 arranged vertically, and the connecting plate 714 passes through the slot 806 Connected with the steel belt 802, the optical inspection module 1 reciprocates in a direction perpendicular to the installation platform 820 under the drive of the steel wire rope 705, and surrounds the installation platform 820 under the drive of the steel belt 802 The peripheral side of the machine reci...
PUM
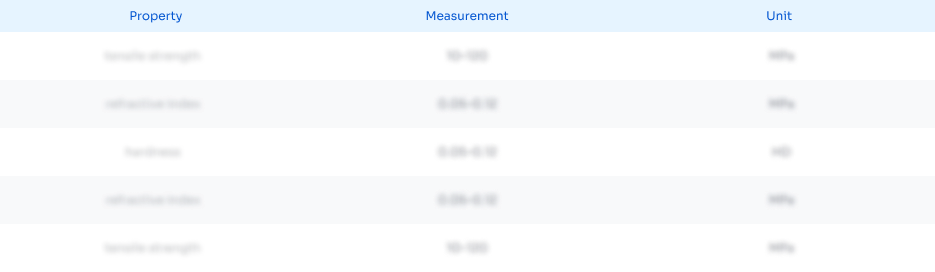
Abstract
Description
Claims
Application Information

- R&D
- Intellectual Property
- Life Sciences
- Materials
- Tech Scout
- Unparalleled Data Quality
- Higher Quality Content
- 60% Fewer Hallucinations
Browse by: Latest US Patents, China's latest patents, Technical Efficacy Thesaurus, Application Domain, Technology Topic, Popular Technical Reports.
© 2025 PatSnap. All rights reserved.Legal|Privacy policy|Modern Slavery Act Transparency Statement|Sitemap|About US| Contact US: help@patsnap.com