Stacking machine and fork positioning method thereof
A stacker and pallet fork technology, which is applied in the field of automated material transportation, can solve the problems that the cargo 72 cannot be fed in, the deformation amount is different, and the pallet fork 71 cannot be accurately inserted into the target position of the shelf, etc.
- Summary
- Abstract
- Description
- Claims
- Application Information
AI Technical Summary
Problems solved by technology
Method used
Image
Examples
specific Embodiment approach 2
[0057] Please also refer to Figure 7 to Figure 9 The difference between this embodiment and the first embodiment is that the load detection module 8 mainly includes a tension sensor 81 , a fastening bolt 83 and a pressing block 85 .
[0058] In this embodiment, the tension sensor 81 includes a housing 811 and two supporting parts 813 protruding from the same side of the housing 811, each supporting part 813 is provided with a slot 801 for clamping the wire rope 35, The compression block 85 is sleeved on the outer periphery of the housing 811 and is located between the two supporting parts 813. There is a gap between the compression block 85 and the housing 811 for the wire rope 35 to pass through. The compression block 85 and the fastening bolt 83 are connected to tighten the wire rope 35. During the working process, due to the effect of the fastening bolt 83, the steel wire rope 35 is kept in a tensioned state. The steel wire rope 35 has pressure on the support portion 813...
PUM
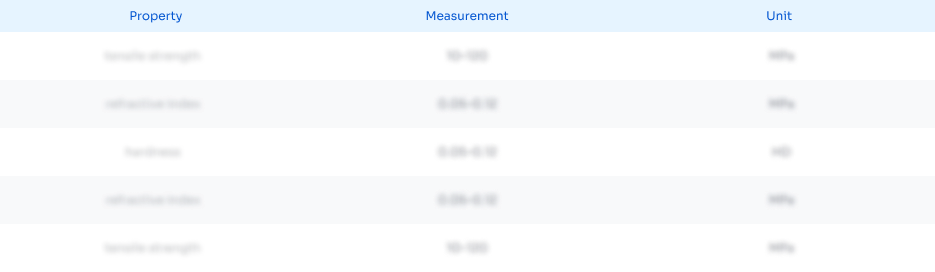
Abstract
Description
Claims
Application Information

- R&D
- Intellectual Property
- Life Sciences
- Materials
- Tech Scout
- Unparalleled Data Quality
- Higher Quality Content
- 60% Fewer Hallucinations
Browse by: Latest US Patents, China's latest patents, Technical Efficacy Thesaurus, Application Domain, Technology Topic, Popular Technical Reports.
© 2025 PatSnap. All rights reserved.Legal|Privacy policy|Modern Slavery Act Transparency Statement|Sitemap|About US| Contact US: help@patsnap.com