Method and system for determining installation position of rate gyroscope
A technology for installing position and rate gyroscopes, applied in geometric CAD, design optimization/simulation, etc., can solve the problems of long and thin structure, increase product cost, and fast change, so as to improve stability margin and reduce high attenuation Demand, the effect of reducing product costs
- Summary
- Abstract
- Description
- Claims
- Application Information
AI Technical Summary
Problems solved by technology
Method used
Image
Examples
Embodiment Construction
[0024] The technical solutions in the embodiments of the present application are clearly and completely described below in combination with the drawings in the embodiments of the present application. Obviously, the described embodiments are part of the embodiments of the present application, not all of them. Based on the embodiments in this application, all other embodiments obtained by those skilled in the art without making creative efforts belong to the scope of protection of this application.
[0025] The present application relates to a method and system for determining the installation position of a rate gyroscope. According to this application, the installation position of the rate gyro is optimized, the demand for high attenuation of the notch filter caused by insufficient elastic suppression control margin is reduced, and the flight stability margin, dynamic characteristics and control accuracy are improved. Use a single-rate gyro per channel to adapt to multi-level f...
PUM
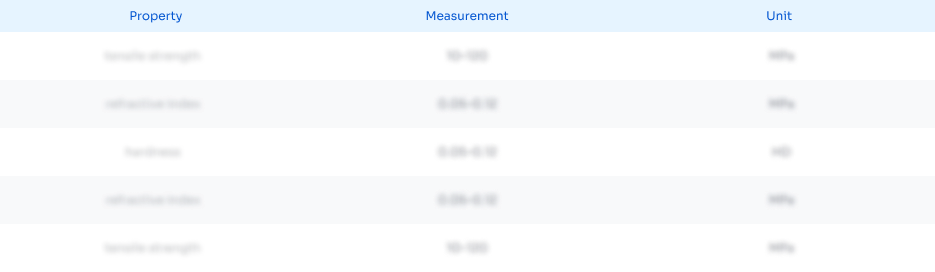
Abstract
Description
Claims
Application Information

- R&D
- Intellectual Property
- Life Sciences
- Materials
- Tech Scout
- Unparalleled Data Quality
- Higher Quality Content
- 60% Fewer Hallucinations
Browse by: Latest US Patents, China's latest patents, Technical Efficacy Thesaurus, Application Domain, Technology Topic, Popular Technical Reports.
© 2025 PatSnap. All rights reserved.Legal|Privacy policy|Modern Slavery Act Transparency Statement|Sitemap|About US| Contact US: help@patsnap.com