A profile rolling automatic production line
An automatic production and assembly line technology, applied in the direction of metal processing equipment, metal processing, manufacturing tools, etc., can solve the problems that affect the quality of the profile section, the deformation of the cutting part, etc.
- Summary
- Abstract
- Description
- Claims
- Application Information
AI Technical Summary
Problems solved by technology
Method used
Image
Examples
Embodiment Construction
[0050] The present invention will be described in further detail below in conjunction with the accompanying drawings.
[0051] to combine figure 1 and figure 2 As shown, it is an automatic production line for profile rolling disclosed by the present invention, which includes an unwinding mechanism 1 arranged sequentially along the conveying direction of the metal strip 6 for continuous unwinding of the metal strip 6, for unwinding the unwinding The pre-processing system 2 for flattening and / or punching the metal strip 6, the side punching mechanism 3 for cutting one or both sides of the metal strip 6 out of the gap 61, and the The post-processing system 4 for the metal strip 6 to be rolled, bent, shaped and / or welded, and the cutting mechanism 5 for cutting and separating the roll-formed profile 63; wherein, the profile 63 roll-pressed automatic production line also includes The processing system 2 , the post-processing system 4 and the cutting mechanism 5 are controlled an...
PUM
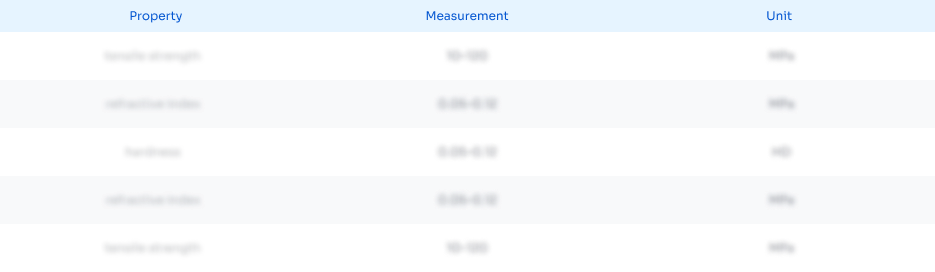
Abstract
Description
Claims
Application Information

- Generate Ideas
- Intellectual Property
- Life Sciences
- Materials
- Tech Scout
- Unparalleled Data Quality
- Higher Quality Content
- 60% Fewer Hallucinations
Browse by: Latest US Patents, China's latest patents, Technical Efficacy Thesaurus, Application Domain, Technology Topic, Popular Technical Reports.
© 2025 PatSnap. All rights reserved.Legal|Privacy policy|Modern Slavery Act Transparency Statement|Sitemap|About US| Contact US: help@patsnap.com