Preparation method of metal plated film for battery
A metal plating and battery technology, applied in battery electrodes, metal material coating processes, circuits, etc., can solve the problems of wrinkling and deformation of the base film, affecting the film quality, etc., to avoid film curling, ensure evaporation quality, and improve Combine the effect of the effect
- Summary
- Abstract
- Description
- Claims
- Application Information
AI Technical Summary
Problems solved by technology
Method used
Image
Examples
Embodiment 1
[0030] A method for preparing a metallized film for a battery, comprising the following steps:
[0031] (1) After taking the base film and carrying out surface treatment on its surface, the first metal layer is deposited on the surface of the base film through a vacuum evaporation chamber filled with metal vapor;
[0032] (2) After treating the base film with the metal layer evaporated, continue to pass through the vacuum evaporation chamber to evaporate the next layer of metal layer;
[0033] (3) According to step (2), cyclically vapor-deposit several layers of metal layers on the base film, so that the thickness of all metal layers meets the set requirements, and the process is completed.
[0034] In step (1), the method of surface treatment of the base film is corona treatment, electric spark treatment, plasma treatment, Ni plating treatment, Al plating 2 o 3 Treatment, chemical treatment coating or NaOH immersion treatment in one or more combination (corona treatment is ...
Embodiment 2
[0055] Compared with Example 1, most of them are the same, except that in this example, the relative humidity is controlled to be 60%.
Embodiment 3
[0057] Compared with Example 1, most of them are the same, except that in this example, the oxygen flow will be sprayed on the lower surface of the base film, and the mixed gas of oxygen and argon (the volume ratio of the two is 1:4) will be used instead. plasma treatment.
[0058] At the same time, the bonding strength of the aluminized films prepared in the above-mentioned Examples 1-Example 3 and Comparative Example 1-Comparative Example 5 was tested, and the obtained performance results are shown in Table 1 below.
[0059] Table 1 Properties of various aluminized films
[0060]
[0061]
[0062] Note: Downstream manufacturers require that the bonding strength of the metal layer of the aluminized film product be ≥ 2N. Generally, 2N is regarded as a qualified product for delivery, and a product greater than 3N is regarded as an excellent product.
[0063] From the measured data in Table 1 above, it can be seen that the bonding strength between the metal layers is grea...
PUM
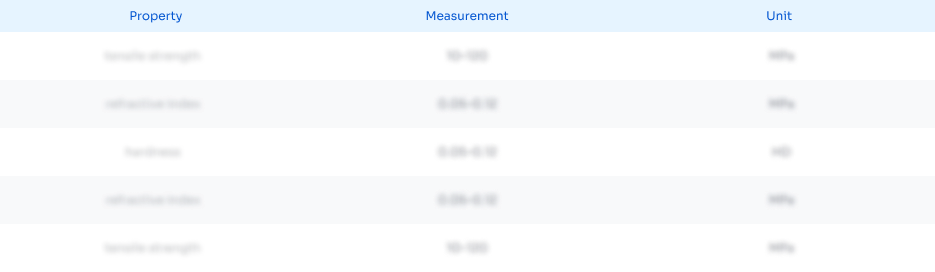
Abstract
Description
Claims
Application Information

- R&D
- Intellectual Property
- Life Sciences
- Materials
- Tech Scout
- Unparalleled Data Quality
- Higher Quality Content
- 60% Fewer Hallucinations
Browse by: Latest US Patents, China's latest patents, Technical Efficacy Thesaurus, Application Domain, Technology Topic, Popular Technical Reports.
© 2025 PatSnap. All rights reserved.Legal|Privacy policy|Modern Slavery Act Transparency Statement|Sitemap|About US| Contact US: help@patsnap.com