A kind of reinforcement method of fiber-reinforced silicon carbide ceramic matrix composite material
A technology of silicon carbide ceramic matrix and composite materials, which is applied in the field of ceramic matrix composite materials, can solve the problems of strength and high temperature oxidation resistance, performance and oxidation resistance, and affect the aesthetics of composite materials, etc., to reduce the risk of falling off , reduce porosity, improve strength
- Summary
- Abstract
- Description
- Claims
- Application Information
AI Technical Summary
Problems solved by technology
Method used
Image
Examples
Embodiment 1
[0024] This implementation is a flat plate with more micropores and coarse pores, and the steps of using the method of the present invention to reinforce are as follows:
[0025] (1) Polish the surface of the flat part with sandpaper to remove fine particles on the surface, and ultrasonically clean it in deionized water for 30 minutes;
[0026] (2) Dry in an oven at 100°C for 1 hour;
[0027] (3) Put the dried plate in the dipping tank, vacuumize to -0.1MPa, and keep it for 30min;
[0028] (4) Weigh 0.5 L of liquid polycarbosilane with a viscosity of 50 cP, pour it into a dipping tank, and dip it for 8 hours;
[0029] (5) Complete cracking in 1000°C vacuum cracking furnace for 2 hours after taking it out;
[0030] (6) Take by weighing 0.5kg liquid polycarbosilane and 0.025kg nano-silicon carbide particles, and mix them uniformly with high-speed stirring;
[0031] (7) Clean the surface of the cracked plate, put it in a dipping tank and vacuumize to -0.1MPa, and keep it for 3...
Embodiment 2
[0042] This embodiment is a workpiece with more surface holes, and the steps of adopting the method of the present invention for reinforcement are as follows:
[0043] (1) Polish the surface of the workpiece with sandpaper to remove fine particles on the surface, and ultrasonically clean it in deionized water for 30 minutes;
[0044] (2) Dry in an oven at 100°C for 1 hour;
[0045] (3) Put the dried plate in the dipping tank, vacuumize to -0.1MPa, and keep it for 60min;
[0046] (4) Weigh 0.2 L of liquid polycarbosilane with a viscosity of 80 cP, pour it into a dipping tank, and dip it for 15 hours;
[0047] (5) After taking it out, complete the cracking in a vacuum cracking furnace at 1300°C for 1 hour;
[0048] (6) Take by weighing 0.2kg liquid polycarbosilane and 0.005kg nano-silicon carbide particles, and mix them uniformly with high-speed stirring;
[0049] (7) Clean up the cracked test sample, put it in the dipping tank and vacuumize it to -0.1MPa, and keep it for 60m...
Embodiment 3
[0060] This embodiment is a part with more fine pores and surface holes, such as figure 1 As shown, the steps of adopting the method of the present invention to reinforce are as follows:
[0061] (1) Polish the surface of the workpiece with sandpaper to remove fine particles on the surface, and ultrasonically clean it in deionized water for 30 minutes;
[0062] (2) Dry in an oven at 100°C for 1 hour;
[0063] (3) Put the dried plate in the dipping tank, vacuumize to -0.1MPa, and keep it for 10min;
[0064] (4) Weigh 0.2 L of liquid polycarbosilane with a viscosity of 30 cP, pour it into a dipping tank, and dip it for 3 hours;
[0065] (5) Complete cracking in 700°C vacuum cracking furnace for 4 hours after taking it out;
[0066] (6) Take by weighing 0.2kg liquid polycarbosilane and 0.04kg nano-silicon carbide particles, and mix them uniformly with high-speed stirring;
[0067] (7) Clean the cracked test sample, put it in the dipping tank and vacuumize it to -0.1MPa, and kee...
PUM
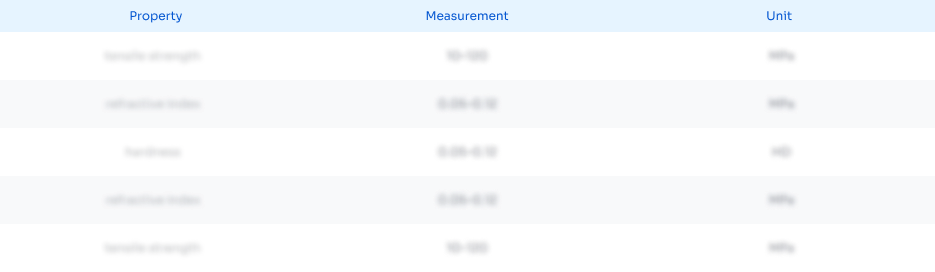
Abstract
Description
Claims
Application Information

- R&D
- Intellectual Property
- Life Sciences
- Materials
- Tech Scout
- Unparalleled Data Quality
- Higher Quality Content
- 60% Fewer Hallucinations
Browse by: Latest US Patents, China's latest patents, Technical Efficacy Thesaurus, Application Domain, Technology Topic, Popular Technical Reports.
© 2025 PatSnap. All rights reserved.Legal|Privacy policy|Modern Slavery Act Transparency Statement|Sitemap|About US| Contact US: help@patsnap.com