Rotor system and micro gas turbine generator set
A rotor and compressor technology, applied in gas turbine installations, machines/engines, mechanical equipment, etc., can solve the problems of poor rotor system stability, coaxiality deviation, coupling damage, etc., and achieve good stability and high verticality. , the effect of long life
- Summary
- Abstract
- Description
- Claims
- Application Information
AI Technical Summary
Problems solved by technology
Method used
Image
Examples
Embodiment 1
[0066] In this embodiment, a motor structure is provided in which the stator winding is wound in a back-winding manner.
[0067] Specifically, such as figure 2 As shown, the motor 600 includes: a motor stator 610, a motor rotor 620 (not shown in this figure), and a motor housing 630. The motor stator 620 is sleeved on the rotating shaft 100 and maintains a certain gap with the rotating shaft 100 in the radial direction. The motor housing 630 is disposed on the outer periphery of the motor stator 410 , and the motor stator 610 is provided with a plurality of air inlets 640 axially penetrating through the motor stator 610 .
[0068] Since the air inlet 640 is provided, the air intake of the compressor 300 can enter the compressor 300 through the air inlet 640, so that the air intake of the compressor 300 is more sufficient, and at the same time, the normal temperature air passing through the air inlet 640 can It also plays a certain role in cooling the motor stator 610.
[00...
Embodiment 2
[0079] In this embodiment, a structure of an integrated bearing 400 is provided. The integrated bearing 400 includes a radial bearing part and a thrust bearing part. The radial bearing part and the thrust bearing part are integrally formed or finished after assembly. Therefore, the radial bearing part The verticality between the central axis of the rotor and the thrust surface of the thrust bearing is high, the rotor system is installed with high precision and runs smoothly.
[0080] Specifically, see Figure 7 , one-piece bearing 400 includes:
[0081] The first thrust plate 410 and the second thrust plate 420 are fixedly installed on the second shaft segment 120, the first thrust plate 410 and the second thrust plate 420 are arranged oppositely, and an annular groove 430 is formed between them;
[0082] The bearing stator 440 is installed in the annular groove 430 and connected with the rotor system housing 450, and there is a first axial clearance between the two end faces...
Embodiment 3
[0102] In this embodiment, an anti-rotation structure for the one-piece bearing 400 in the second embodiment is provided. The bearing stator 440 of the integrated bearing 400 is installed in the rotor system housing 450 and the rotor system end cover 460, the rotor system housing 450 is sleeved on the circumference of the bearing stator 440 and one end surface, and the rotor system end cover 460 is sleeved on the rotating shaft 100 and located on the other end surface of the bearing stator 440 to realize the axial limit of the other side of the bearing stator 440. An anti-rotation member is arranged between the rotor system housing 450 and the bearing stator 440, and the anti-rotation member is used to realize the circumferential positioning of the bearing stator 440 relative to the rotor system housing 450, so as to prevent the bearing stator 440 from moving with the first thrust plate 410 or the second thrust plate 410. Thrust plate 420 rotates.
[0103] Specifically, one e...
PUM
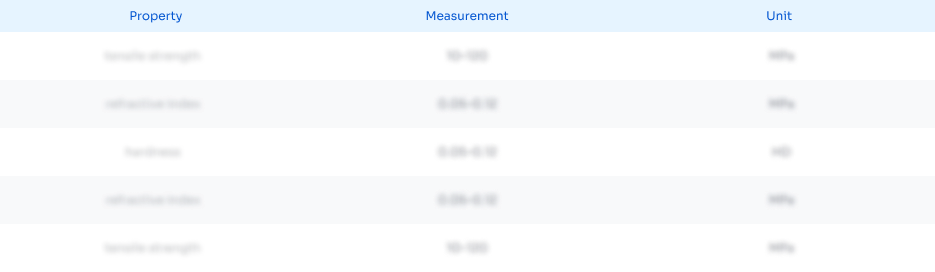
Abstract
Description
Claims
Application Information

- R&D Engineer
- R&D Manager
- IP Professional
- Industry Leading Data Capabilities
- Powerful AI technology
- Patent DNA Extraction
Browse by: Latest US Patents, China's latest patents, Technical Efficacy Thesaurus, Application Domain, Technology Topic, Popular Technical Reports.
© 2024 PatSnap. All rights reserved.Legal|Privacy policy|Modern Slavery Act Transparency Statement|Sitemap|About US| Contact US: help@patsnap.com