Grouping injection molding method
An indexing and injection molding technology, which is applied to household components, household appliances, and other household appliances, can solve the problems of increased design and production costs, complicated process flow, and high production costs, so as to save the time and storage volume of glue curing Many, the effect of reducing the cost of injection molding
- Summary
- Abstract
- Description
- Claims
- Application Information
AI Technical Summary
Problems solved by technology
Method used
Image
Examples
Embodiment Construction
[0015] A method of indexing injection molding, see Figure 1-Figure 2 : The top of the rotor to be injected is evenly distributed with M injection holes, the rotor to be injected is placed in the cavity of the lower mold 1, and the injection outlet of the upper mold 2 is aligned with the continuously arranged L injection holes. Where M=N×L, the bottom of the lower mold 1 is placed on the servo turntable 3, and the servo turntable 3 is driven to rotate by the servo motor to complete the injection molding of L injection holes in a single time, and then the servo motor circulates the corresponding preset rotation angle , carry out the injection molding of the next group of L injection holes until the injection molding of all the injection holes on the top of the rotor is completed, and then the mold is opened and the rotor is taken out.
[0016] The material inlet 21 of the upper mold 2 is arranged on the side, the plastic injection cylinder 4 is arranged on one side of the upper...
PUM
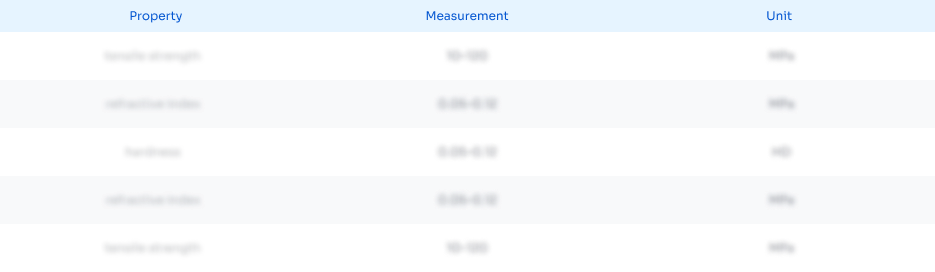
Abstract
Description
Claims
Application Information

- Generate Ideas
- Intellectual Property
- Life Sciences
- Materials
- Tech Scout
- Unparalleled Data Quality
- Higher Quality Content
- 60% Fewer Hallucinations
Browse by: Latest US Patents, China's latest patents, Technical Efficacy Thesaurus, Application Domain, Technology Topic, Popular Technical Reports.
© 2025 PatSnap. All rights reserved.Legal|Privacy policy|Modern Slavery Act Transparency Statement|Sitemap|About US| Contact US: help@patsnap.com