Horizontal multi-joint robot
A horizontal multi-joint, robot technology, applied in the field of robotics, can solve the problems of reducing the robot's running speed and beat, increasing the weight and moment of inertia of the robot arm, etc., to reduce the weight and moment of inertia, improve the running speed and beat, and reduce the volume Effect
- Summary
- Abstract
- Description
- Claims
- Application Information
AI Technical Summary
Problems solved by technology
Method used
Image
Examples
Embodiment 1
[0060] Example 1 works like this:
[0061] The first motor 11 drives the first transmission shaft 222 to rotate through the first synchronous belt 15 and the first transmission pulley 226, and drives the driving arm 3 to rotate around the J1 axis; the driving arm 3 drives the small arm assembly 5 to rotate around the J2 axis through the attached rod 31.
[0062] The second motor 12 drives the second transmission shaft 223 to rotate through the second synchronous belt 16 and the second transmission pulley 227, and drives the boom assembly 4 to rotate around the J1 axis.
[0063] The third motor 13 drives the third transmission shaft 224 to rotate through the third synchronous belt 17 and the third transmission pulley 228. The arm driven pulley 441, the second connecting shaft 72, the first small arm driving pulley 54, the first small arm synchronous belt 52, and the first small arm driven pulley 541 drive the lifting nut 62 to rotate, and drive the execution shaft 61 to move up...
PUM
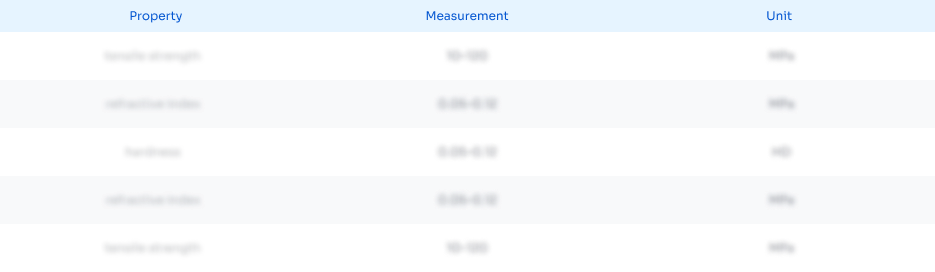
Abstract
Description
Claims
Application Information

- Generate Ideas
- Intellectual Property
- Life Sciences
- Materials
- Tech Scout
- Unparalleled Data Quality
- Higher Quality Content
- 60% Fewer Hallucinations
Browse by: Latest US Patents, China's latest patents, Technical Efficacy Thesaurus, Application Domain, Technology Topic, Popular Technical Reports.
© 2025 PatSnap. All rights reserved.Legal|Privacy policy|Modern Slavery Act Transparency Statement|Sitemap|About US| Contact US: help@patsnap.com