Steam turbine rotor system instability limit rapid prediction method based on shroud ring zero damping
A steam turbine rotor, zero damping technology, used in the testing of machine/structural components, static/dynamic balance testing, measuring devices, etc., can solve the problems of large error, complex vibration, inability to accurately obtain the shroud and the entire rotor system, etc.
- Summary
- Abstract
- Description
- Claims
- Application Information
AI Technical Summary
Problems solved by technology
Method used
Image
Examples
Embodiment 1
[0028] Embodiment 1. This embodiment provides a rapid prediction method for the instability limit of the steam turbine rotor system based on zero damping of the shroud;
[0029] A rapid prediction method for the instability limit of the steam turbine rotor system based on the zero damping of the shroud, including:
[0030] S1: Construct the equivalent model of the shroud damping of the steam turbine rotor system under multi-frequency excitation and the quantitative calculation formula of the shroud damping;
[0031] S2: According to the structure of the steam turbine rotor system, calculate the modal mass of the steam turbine rotor system and the natural frequency ignoring the shroud damping;
[0032] S3: Use flow field simulation to obtain the multi-frequency excitation force of the steam turbine rotor system under a certain operating condition, convert the multi-frequency excitation force into the superposition of harmonic excitation components of multiple orders and differe...
PUM
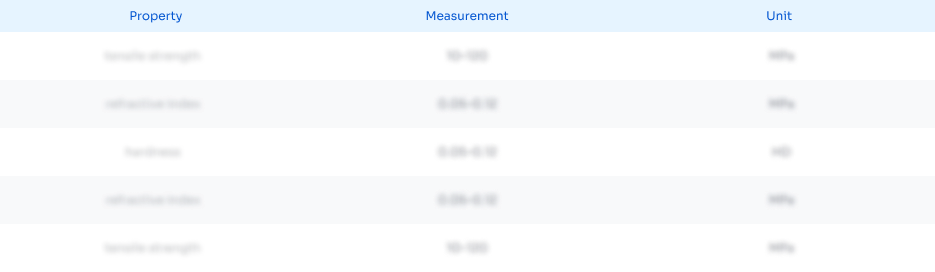
Abstract
Description
Claims
Application Information

- Generate Ideas
- Intellectual Property
- Life Sciences
- Materials
- Tech Scout
- Unparalleled Data Quality
- Higher Quality Content
- 60% Fewer Hallucinations
Browse by: Latest US Patents, China's latest patents, Technical Efficacy Thesaurus, Application Domain, Technology Topic, Popular Technical Reports.
© 2025 PatSnap. All rights reserved.Legal|Privacy policy|Modern Slavery Act Transparency Statement|Sitemap|About US| Contact US: help@patsnap.com