Method and device for predicting fatigue crack propagation direction of aircraft structure
A technology of fatigue crack growth and aircraft structure, applied in the direction of instruments, electrical digital data processing, geometric CAD, etc., can solve problems affecting the safety of aircraft use
- Summary
- Abstract
- Description
- Claims
- Application Information
AI Technical Summary
Problems solved by technology
Method used
Image
Examples
Embodiment
[0057] The present invention will be further described in detail with a specific example below.
[0058] A method for predicting the direction of fatigue crack growth in aircraft structures based on finite elements, comprising the following steps:
[0059] It is known that the thickness of a skin structure is t=1mm, the crack length a=20mm, and the material of the skin structure is 2024.
[0060] Predict the fatigue crack growth direction of the aircraft skin structure.
[0061] Step 1: Establish a static strength finite element model. Reasonably select the structural analysis area, select the appropriate unit type, simulate the support and constraints of the structure, apply real loads, and establish a static strength finite element model.
[0062] Step 2, establishing a finite element model of the structure containing cracks. In the static strength finite element model established in step 1, cracks are introduced according to the real crack trajectory curve, the initial c...
PUM
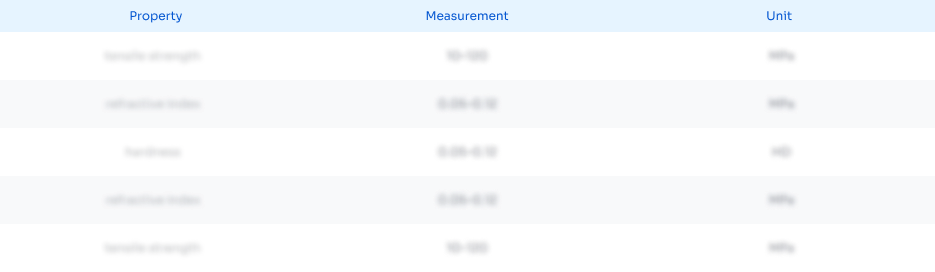
Abstract
Description
Claims
Application Information

- Generate Ideas
- Intellectual Property
- Life Sciences
- Materials
- Tech Scout
- Unparalleled Data Quality
- Higher Quality Content
- 60% Fewer Hallucinations
Browse by: Latest US Patents, China's latest patents, Technical Efficacy Thesaurus, Application Domain, Technology Topic, Popular Technical Reports.
© 2025 PatSnap. All rights reserved.Legal|Privacy policy|Modern Slavery Act Transparency Statement|Sitemap|About US| Contact US: help@patsnap.com