Method for determining theoretical value dispersion coefficient of crack forming life of aircraft structure
A dispersion coefficient and aircraft structure technology, applied in the field of aviation fatigue fracture, can solve problems such as the difference between the theoretical calculation value of fatigue life and the fatigue life test value, the instability of the manufacturing process of structural parts, and the instability of material properties, etc., to achieve clear steps , correct theoretical analysis method and clear engineering concept
- Summary
- Abstract
- Description
- Claims
- Application Information
AI Technical Summary
Problems solved by technology
Method used
Image
Examples
specific Embodiment
[0067] The specific implementation of the method for determining the dispersion coefficient of the theoretical value of the crack formation life of the aircraft structure provided by the embodiment of the present invention will be further described in detail below with a specific embodiment.
[0068] This specific embodiment provides a method for determining the dispersion coefficient of the theoretical value of the aircraft structure crack formation life based on the test, and the specific implementation is as follows:
[0069] Known: A fatigue damage tolerance test piece, the structure does not contain initial cracks, the test lasts from the fatigue test to the final fracture, and the total number of cycles N=87500 is recorded.
[0070] The method for determining the dispersion coefficient of the aircraft structure crack formation life theoretical value based on the test provided by this specific embodiment includes the following steps:
[0071] Step 1, establishing a coordi...
PUM
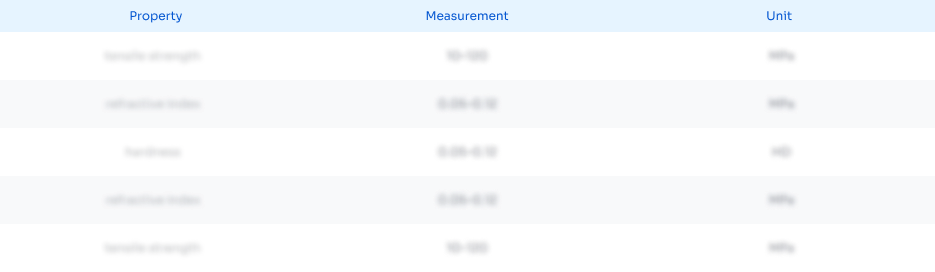
Abstract
Description
Claims
Application Information

- R&D
- Intellectual Property
- Life Sciences
- Materials
- Tech Scout
- Unparalleled Data Quality
- Higher Quality Content
- 60% Fewer Hallucinations
Browse by: Latest US Patents, China's latest patents, Technical Efficacy Thesaurus, Application Domain, Technology Topic, Popular Technical Reports.
© 2025 PatSnap. All rights reserved.Legal|Privacy policy|Modern Slavery Act Transparency Statement|Sitemap|About US| Contact US: help@patsnap.com