Machine tool thermal error prediction method and system based on temperature sensitive interval segmentation
A prediction method and thermal error technology, applied in the field of predicting the thermal error of machine tools, can solve problems such as fluctuations in prediction performance, and achieve the effects of strong versatility, improved prediction robustness, and improved prediction accuracy.
- Summary
- Abstract
- Description
- Claims
- Application Information
AI Technical Summary
Problems solved by technology
Method used
Image
Examples
Embodiment Construction
[0035] The present invention will be further described in detail below in conjunction with the accompanying drawings and preferred embodiments.
[0036] The overall process reference of this specific implementation figure 1 as shown, figure 1 The first four steps in are the specific refinement process for obtaining the temperature sensitive range. Each part is described in detail below.
[0037] 1. Data collection
[0038] The data acquisition system includes an infrared thermal imager, a temperature sensor group and an eddy current displacement sensor;
[0039] Infrared thermal imager is used to make a thermal image of the machine tool to obtain the temperature color image characteristics of the machine tool; according to the temperature color image characteristics displayed by the thermal imager, the heat source area of the machine tool can be manually marked;
[0040]The temperature sensor group is set separately at the heat source area of the manual marking machine...
PUM
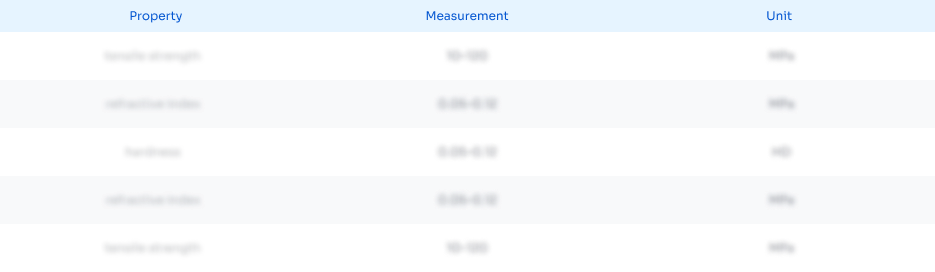
Abstract
Description
Claims
Application Information

- R&D
- Intellectual Property
- Life Sciences
- Materials
- Tech Scout
- Unparalleled Data Quality
- Higher Quality Content
- 60% Fewer Hallucinations
Browse by: Latest US Patents, China's latest patents, Technical Efficacy Thesaurus, Application Domain, Technology Topic, Popular Technical Reports.
© 2025 PatSnap. All rights reserved.Legal|Privacy policy|Modern Slavery Act Transparency Statement|Sitemap|About US| Contact US: help@patsnap.com