Rotor screen preparing device
A technology for preparing device and screen mesh, applied in the field of stainless steel rotor screen mesh preparation device, can solve the problems of large dust flying, large centrifugal speed and gas vorticity, easy deformation, etc. The effect of high production efficiency
- Summary
- Abstract
- Description
- Claims
- Application Information
AI Technical Summary
Problems solved by technology
Method used
Image
Examples
Embodiment Construction
[0037] In the following, the present invention will be further described in detail according to the accompanying drawings and specific embodiments.
[0038] Such as Figure 1-9 As shown, a rotor screen preparation device includes a positioning mandrel 1, a rotor screen assembly 2, a welding locking mechanism 3, a lathe spindle chuck 4, a lathe spindle box 5, a four-jaw chuck device 6, a pull-out Die mechanism7.
[0039] Such as figure 1 As shown, the positioning mandrel 1 of this embodiment is cast from ductile iron, the hollow structure has a wall thickness of 10 mm, an outer diameter of 200 mm, a fit tolerance of H7 level is preferred, and a length of 250 mm. Large threaded holes 101 and Small threaded holes, among them, there is a stepped positioning hole at 101 of the large threaded hole to match the lathe spindle chuck. The diameter of the stepped hole is 116mm, and the fit tolerance is preferably H7. The depth of the stepped hole is 5mm. There are 4 threads arranged ar...
PUM
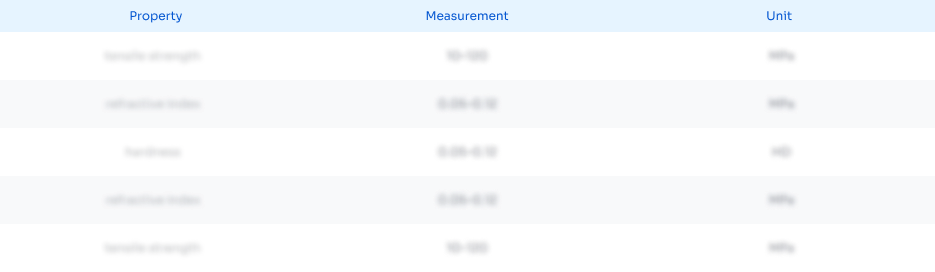
Abstract
Description
Claims
Application Information

- R&D
- Intellectual Property
- Life Sciences
- Materials
- Tech Scout
- Unparalleled Data Quality
- Higher Quality Content
- 60% Fewer Hallucinations
Browse by: Latest US Patents, China's latest patents, Technical Efficacy Thesaurus, Application Domain, Technology Topic, Popular Technical Reports.
© 2025 PatSnap. All rights reserved.Legal|Privacy policy|Modern Slavery Act Transparency Statement|Sitemap|About US| Contact US: help@patsnap.com