Bottom slag dismounting device used for aluminum-zinc pot and application method of bottom slag dismounting device
A technology of aluminum-zinc and slag blocks, which is applied in the direction of transportation and packaging, trolley cranes, cranes, etc., can solve the problems of affecting the quality of the board surface, troublesome removal, and degradation of the board surface quality
- Summary
- Abstract
- Description
- Claims
- Application Information
AI Technical Summary
Problems solved by technology
Method used
Image
Examples
Embodiment Construction
[0030] The present invention will be further described below in conjunction with the accompanying drawings and specific embodiments.
[0031] As shown in the figure, the present invention provides a bottom dross removal device for aluminum-zinc pots, including a coating tank 1, the bottom dross is located at the bottom of the coating tank 1, and it also includes at least one bottom dross dividing part 2 and pre-embedded The hook 3, the bottom slag dividing part 2 divides the bottom slag into a plurality of bottom slag blocks 4, the lower end of the embedded hook 3 is located in the bottom slag block 4, and the upper end of the embedded hook 3 extends Above the bottom slag block 4, the advantage of the present invention is that the liquid in the coating tank 1 is first extracted (baked out) to the height position of the bottom slag, and then the embedded hook 3 will be placed under the liquid heating state (600 ° C ~ 700 ° C). Put the bottom slag and the bottom slag part 2 into...
PUM
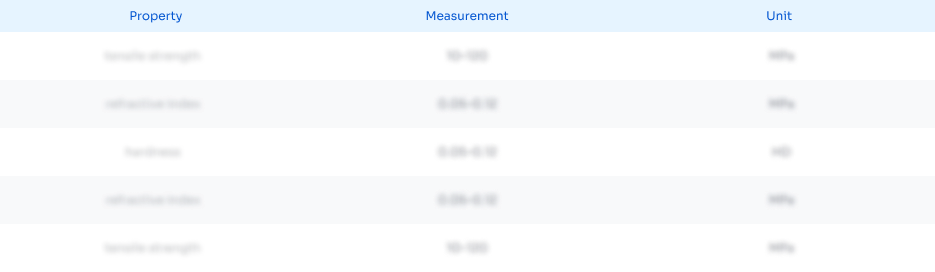
Abstract
Description
Claims
Application Information

- R&D
- Intellectual Property
- Life Sciences
- Materials
- Tech Scout
- Unparalleled Data Quality
- Higher Quality Content
- 60% Fewer Hallucinations
Browse by: Latest US Patents, China's latest patents, Technical Efficacy Thesaurus, Application Domain, Technology Topic, Popular Technical Reports.
© 2025 PatSnap. All rights reserved.Legal|Privacy policy|Modern Slavery Act Transparency Statement|Sitemap|About US| Contact US: help@patsnap.com