Preparation method of multi-material laminated electrode
A multilayer electrode, multi-material technology, applied in electrode manufacturing, electric processing equipment, manufacturing tools, etc., can solve the problems of reducing the service life of tool electrodes, large loss of tiny electrodes, loss, etc., to achieve good processing stability and processing efficiency. High, long service life effect
- Summary
- Abstract
- Description
- Claims
- Application Information
AI Technical Summary
Problems solved by technology
Method used
Image
Examples
preparation example Construction
[0032] refer to figure 1 , showing a method for preparing a multi-material laminated electrode of the present invention, including:
[0033] S110, stacking and combining a first preset number of first metal foils and a second preset number of second metal foils to form a metal laminate; wherein, the resistivity of the first metal foil is greater than the resistivity of the second metal foil ;
[0034] S120, performing a first processing on the metal stack;
[0035] S130, performing a second processing on the metal stack by using preset parameters to form an electrode blank;
[0036] S140, performing electric discharge machining on the electrode blank to form a preset working surface profile, and obtain a target electrode.
[0037] Compared with the prior art, the embodiments of the present invention include the following advantages:
[0038] In the embodiment of the present invention, a metal laminate is formed by laminating and combining a first preset number of first met...
PUM
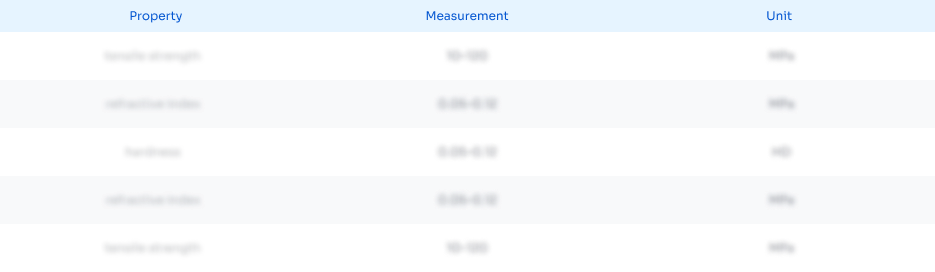
Abstract
Description
Claims
Application Information

- R&D Engineer
- R&D Manager
- IP Professional
- Industry Leading Data Capabilities
- Powerful AI technology
- Patent DNA Extraction
Browse by: Latest US Patents, China's latest patents, Technical Efficacy Thesaurus, Application Domain, Technology Topic, Popular Technical Reports.
© 2024 PatSnap. All rights reserved.Legal|Privacy policy|Modern Slavery Act Transparency Statement|Sitemap|About US| Contact US: help@patsnap.com