Automatic punching and bending device for filter element end covers
A stamping bending and end cap technology, applied in the field of stamping, can solve the problems of affecting the processing speed, affecting the processing accuracy of the filter element end cap, single function, etc., and achieve the effect of a stable stamping process
- Summary
- Abstract
- Description
- Claims
- Application Information
AI Technical Summary
Problems solved by technology
Method used
Image
Examples
Embodiment Construction
[0021] The preferred embodiments of the present invention will be described in detail below in conjunction with the accompanying drawings, so that the advantages and features of the present invention can be more easily understood by those skilled in the art, so as to define the protection scope of the present invention more clearly.
[0022] The automatic stamping and bending device of the filter element end cover of the present invention is suitable for figure 1 In the stamping of the shown end cap, a through central hole 101 is provided in the middle of the filter element end cap, a flange 102 extending downward is provided around the central hole 101, and an edge portion 103 of the filter element end cap extends downward.
[0023] see figure 2 As shown, the automatic punching and bending device for the filter element end cover of the present invention includes a workbench 1 and a gantry 2 connected to the workbench 1 and arranged above it, a first stamping module, a lower ...
PUM
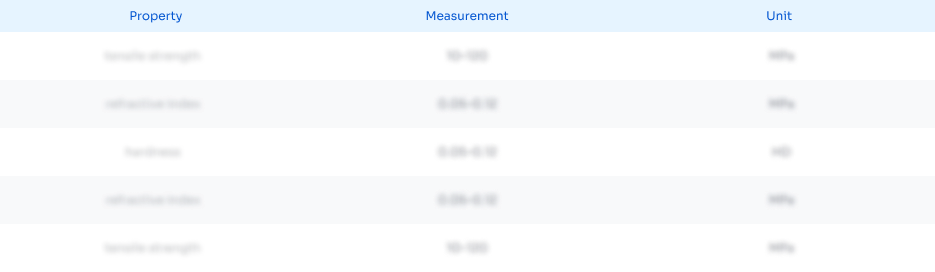
Abstract
Description
Claims
Application Information

- R&D
- Intellectual Property
- Life Sciences
- Materials
- Tech Scout
- Unparalleled Data Quality
- Higher Quality Content
- 60% Fewer Hallucinations
Browse by: Latest US Patents, China's latest patents, Technical Efficacy Thesaurus, Application Domain, Technology Topic, Popular Technical Reports.
© 2025 PatSnap. All rights reserved.Legal|Privacy policy|Modern Slavery Act Transparency Statement|Sitemap|About US| Contact US: help@patsnap.com