A double-cross beam three-dimensional force sensor based on fiber grating
A fiber grating and sensor technology, applied in the field of multi-dimensional force sensing, can solve problems such as complex structure, low sensor sensitivity, strong electromagnetic interference, etc.
- Summary
- Abstract
- Description
- Claims
- Application Information
AI Technical Summary
Problems solved by technology
Method used
Image
Examples
Embodiment Construction
[0030] The following will clearly and completely describe the technical solutions in the embodiments of the present invention in conjunction with the accompanying drawings of the present invention; obviously, the described embodiments are only some of the embodiments of the present invention, not all of them. All other embodiments obtained by persons of ordinary skill in the art without creative efforts fall within the protection scope of the present invention.
[0031] like Figure 1 to Figure 4 As shown: this embodiment provides a fiber grating-based double cross-beam three-dimensional force sensor, including an upper elastic disc 1, a lower elastic disc 2, a force transmission column 3 and a fiber grating assembly.
[0032] The upper elastic disk 1 includes a disk body I11 with a cavity 12 inside and a plane strain beam I located in the cavity 12. The plane strain beam I is in a cross-shaped structure and has four branch beams I13. The outer end of the branch beam I13 (the...
PUM
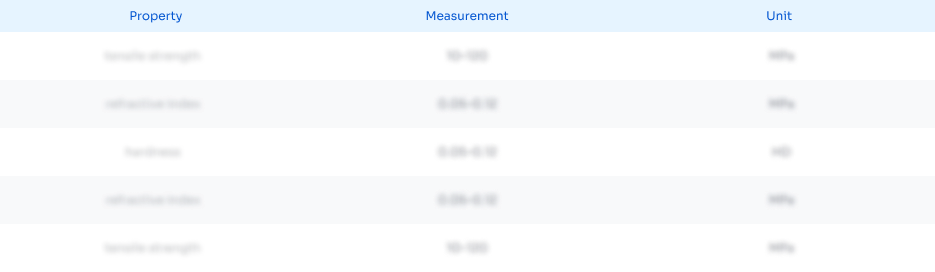
Abstract
Description
Claims
Application Information

- R&D Engineer
- R&D Manager
- IP Professional
- Industry Leading Data Capabilities
- Powerful AI technology
- Patent DNA Extraction
Browse by: Latest US Patents, China's latest patents, Technical Efficacy Thesaurus, Application Domain, Technology Topic, Popular Technical Reports.
© 2024 PatSnap. All rights reserved.Legal|Privacy policy|Modern Slavery Act Transparency Statement|Sitemap|About US| Contact US: help@patsnap.com