Parallel synchronous orthogonal turn-milling flutter stability lobe graph prediction method
A stable lobe diagram, orthogonal turning and milling technology, applied in the field of mechanical processing and manufacturing, can solve the problems of inapplicability and inapplicability of the turning-milling chatter prediction model
- Summary
- Abstract
- Description
- Claims
- Application Information
AI Technical Summary
Problems solved by technology
Method used
Image
Examples
Embodiment Construction
[0059] The present invention will be described in detail below with reference to the accompanying drawings and examples.
[0060] A method for predicting lobe diagrams of chatter stability in parallel synchronous and orthogonal turning and milling, such as figure 1 As shown, the flow chart of constructing the parallel synchronous orthogonal turning and milling stability lobe diagram, the main steps are as follows:
[0061] Step 1: Analyze the multi-degree-of-freedom vibration model of parallel synchronous orthogonal turning and milling;
[0062] Such as figure 2 As shown, the parallel synchronous orthogonal turning and milling process consists of two end mills orthogonally turning and milling the outer contour of the workpiece 5, the end mill I4 and the end mill II6 orthogonally turning and milling the surface of the workpiece 5 at the same time, the speed of the tool in the feed direction There is consistency, but the depth of cut can be different for end mill I4 and end ...
PUM
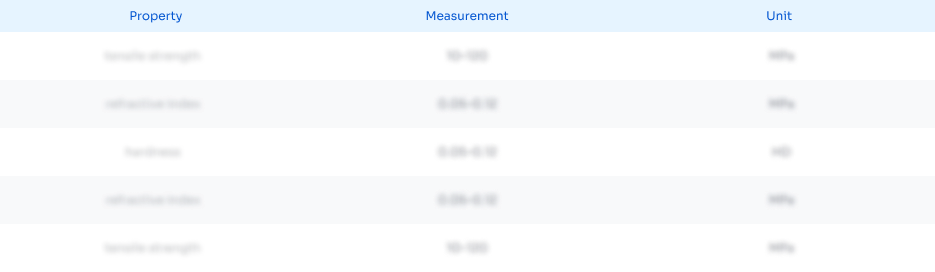
Abstract
Description
Claims
Application Information

- R&D
- Intellectual Property
- Life Sciences
- Materials
- Tech Scout
- Unparalleled Data Quality
- Higher Quality Content
- 60% Fewer Hallucinations
Browse by: Latest US Patents, China's latest patents, Technical Efficacy Thesaurus, Application Domain, Technology Topic, Popular Technical Reports.
© 2025 PatSnap. All rights reserved.Legal|Privacy policy|Modern Slavery Act Transparency Statement|Sitemap|About US| Contact US: help@patsnap.com