Method for filling vertical surface area on back edge of wind power blade
A filling method and area filling technology, which can be applied to other household appliances, household appliances, household components, etc., can solve the problems of narrow and flat cavity structure, hanging glass fiber cloth in the shell, and easy wrinkling of bonding corners. Simple and reasonable design, eliminate resin-rich defects, and improve the effect of bonding strength
- Summary
- Abstract
- Description
- Claims
- Application Information
AI Technical Summary
Problems solved by technology
Method used
Image
Examples
Embodiment Construction
[0020] In order to better understand the purpose, structure and function of the present invention, a method for filling the elevation area of the trailing edge of a wind turbine blade according to the present invention will be further described in detail below in conjunction with the accompanying drawings.
[0021] Such as figure 1 As shown, it is shown as a method for filling the trailing edge elevation area of a wind power blade according to the present invention, which is used to adjust the mold clamping gap in the trailing edge elevation area of the blade. The filling method includes:
[0022] First, before laying the shell outer skin 3, the cladding layer 2 is laid on the corresponding position of the rear edge elevation of the shell on the SS surface and / or the PS surface.
[0023] Specifically, the coating layer 2 is two layers of biaxial cloth, which is laid on the surface of the mold groove at the elevation of the trailing edge of the blade, and covers the cushi...
PUM
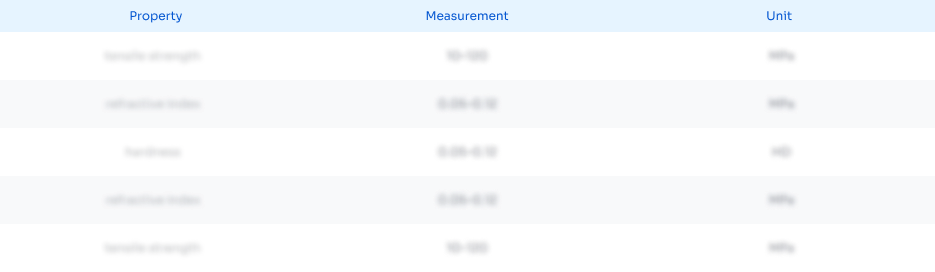
Abstract
Description
Claims
Application Information

- R&D
- Intellectual Property
- Life Sciences
- Materials
- Tech Scout
- Unparalleled Data Quality
- Higher Quality Content
- 60% Fewer Hallucinations
Browse by: Latest US Patents, China's latest patents, Technical Efficacy Thesaurus, Application Domain, Technology Topic, Popular Technical Reports.
© 2025 PatSnap. All rights reserved.Legal|Privacy policy|Modern Slavery Act Transparency Statement|Sitemap|About US| Contact US: help@patsnap.com