Cutting Method of Cylindrical Thin-Walled Casting Shell to Avoid Stress Concentration and Release
A cylindrical, thin-walled technology
- Summary
- Abstract
- Description
- Claims
- Application Information
AI Technical Summary
Problems solved by technology
Method used
Examples
Embodiment Construction
[0017] The present invention is described in detail below:
[0018] A method for splitting and cutting a cylindrical thin-walled casting shell to avoid stress concentration release, comprising the following steps:
[0019] The first step is to install the inner cavity supporting tooling in the inner cavity of the cylindrical thin-walled casting shell, clamp the cylindrical thin-walled casting shell with the inner cavity supporting tooling on the lathe, and cast the cylindrical thin-walled The outer surface of the shell is subjected to rough turning. During rough turning, the cutting depth should not be greater than 0.1mm;
[0020] Step 2: After the rough turning of the outer surface of the cylindrical thin-walled casting shell is completed, remove the inner cavity support tooling, place the rough-turned cylindrical thin-walled casting shell into the vacuum tempering furnace, and start the vacuum tempering furnace , so that the temperature in the furnace rises to 150 degrees C...
PUM
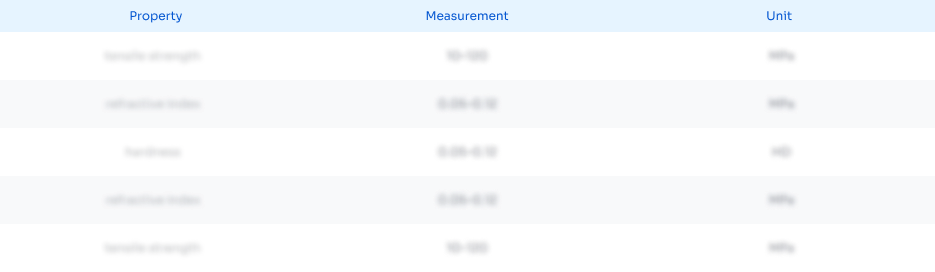
Abstract
Description
Claims
Application Information

- Generate Ideas
- Intellectual Property
- Life Sciences
- Materials
- Tech Scout
- Unparalleled Data Quality
- Higher Quality Content
- 60% Fewer Hallucinations
Browse by: Latest US Patents, China's latest patents, Technical Efficacy Thesaurus, Application Domain, Technology Topic, Popular Technical Reports.
© 2025 PatSnap. All rights reserved.Legal|Privacy policy|Modern Slavery Act Transparency Statement|Sitemap|About US| Contact US: help@patsnap.com