Method for removing trace amount of antimony oxide in coarse bismuth oxide
A bismuth oxide and antimony oxide technology, applied in chemical instruments and methods, inorganic chemistry, bismuth compounds, etc., can solve the problems of long process flow and large loss of raw materials, and achieve short process flow, less consumption of auxiliary materials, and reduced loss of bismuth oxide. Effect
- Summary
- Abstract
- Description
- Claims
- Application Information
AI Technical Summary
Problems solved by technology
Method used
Image
Examples
Embodiment 1
[0019] Raw material coarse bismuth oxide (≥99.0%), Sb 2 o 3 : 0.064%, other impurities (such as Zn, Ca, Pb, Cu, etc.) are less than 10ppm, at 90 ℃, coarse bismuth oxide: water = 1:10, stirring for 2h, 1 filter, Sb is reduced to 0.019% , repeat the above operation, Sb is reduced to 0.001%.
Embodiment 2
[0021] Raw material coarse bismuth oxide (≥99.0%), Sb 2 o 3 : 0.96%, other impurities (such as Zn, Ca, Pb, Cu, etc.) are less than 10ppm, at a temperature of 80 ℃, coarse bismuth oxide: lye (sodium hydroxide concentration is 0.5%) = 1:10, stirring for 3h , filtered once, rinsed with water at 60°C for 0.5h, Sb: 0.0008%, Na: 0.0007%.
PUM
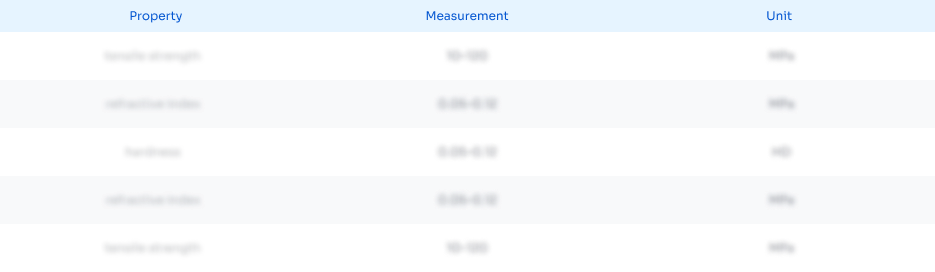
Abstract
Description
Claims
Application Information

- Generate Ideas
- Intellectual Property
- Life Sciences
- Materials
- Tech Scout
- Unparalleled Data Quality
- Higher Quality Content
- 60% Fewer Hallucinations
Browse by: Latest US Patents, China's latest patents, Technical Efficacy Thesaurus, Application Domain, Technology Topic, Popular Technical Reports.
© 2025 PatSnap. All rights reserved.Legal|Privacy policy|Modern Slavery Act Transparency Statement|Sitemap|About US| Contact US: help@patsnap.com