Ultrasonic coaxial assisted dual-shaft-shoulder friction stir welding method
A friction stir welding and friction stir technology, which is applied in welding equipment, non-electric welding equipment, metal processing equipment, etc., can solve the problems of affecting the strength of joints, large heat affected zone of the weld, and reducing the service life of the stirring head. The effect of utilization
- Summary
- Abstract
- Description
- Claims
- Application Information
AI Technical Summary
Problems solved by technology
Method used
Image
Examples
Embodiment 1
[0028] combine figure 1 , a method for ultrasonic coaxially assisted double-shoulder friction stir welding, comprising the following steps:
[0029] (1) The workpiece 1 to be welded is placed on the welding platform in the form of butt joint, and the two are clamped and fixed with a tooling fixture to ensure that the two do not move staggered during the welding process.
[0030] (2) Adjust the position of the stirring needle 3 of the double-shoulder friction stir welding stirring head so that it is aligned with the butt joint of the workpiece 1, and then adjust the ultrasonic tool at the bottom of the lower shoulder 4 of the double-shoulder friction stir welding stirring head The position of the ultrasonic tool head 5 is coaxial with the lower shaft shoulder 4, and a small upward pressure (0.1MPa-1MPa) is applied to the ultrasonic tool head 5 to make the ultrasonic tool head 5 The head 5 and the lower shoulder 4 are in a pressed state during the welding process.
[0031] (3)...
PUM
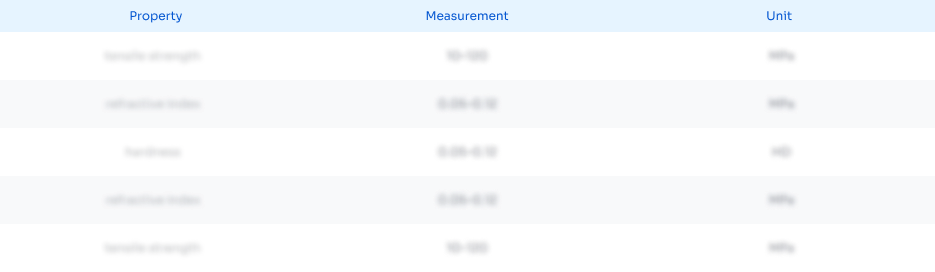
Abstract
Description
Claims
Application Information

- R&D
- Intellectual Property
- Life Sciences
- Materials
- Tech Scout
- Unparalleled Data Quality
- Higher Quality Content
- 60% Fewer Hallucinations
Browse by: Latest US Patents, China's latest patents, Technical Efficacy Thesaurus, Application Domain, Technology Topic, Popular Technical Reports.
© 2025 PatSnap. All rights reserved.Legal|Privacy policy|Modern Slavery Act Transparency Statement|Sitemap|About US| Contact US: help@patsnap.com